Process Mining - Have We Found Gold? by Wilmer Pereira, Salesforce
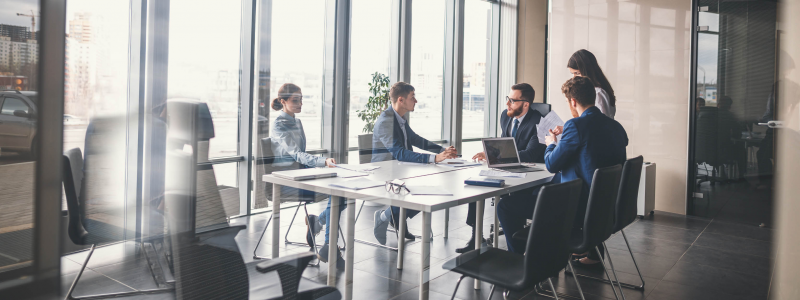
Wilmer Pereira is a certified Lean Six Sigma Master Black Belt with more than 15 years of experience in process improvement. Currently working as the Senior Manager of Process Innovation for customer success platform Salesforce, Wilmer is leading and managing Operation Excellence project portfolios to accomplish measurable business improvements. Below, he shares how his attendance at last year's edition of OPEX Week provided him with some much needed for thought regarding the application of process mining.
I’m recently back from a productive week in Orlando for OPEX Week 2019. Eager to catch up on developments after being absent from the business transformation summit the previous year, I hit the workshops, interactive discussion groups, and case study sessions with gusto. One topic that got me particularly excited was process mining.
If you’re in the process innovation field, you’ve probably been on a Lean Six Sigma team experiencing frustration from executives who don’t want to wait months for the team to collect, sift through, and make sense of a mountain of data. Some executives get impatient enough to jump into a solution before analysis of the data is complete, and this often leads to problematic results due to a poorly informed decision.
I’ve seen this situation in the past, and that’s why my encounter with process mining at OPEX Week got me especially intrigued—and hopeful!
What Is It?
If you’ve heard about process mining, you’ve perhaps encountered the term first in connection with robotic process automation (RPA) technology. For businesses and organizations, RPA holds undeniable potential for productivity and efficiency gains. An RPA bot, for example, can release workers from many repetitive and manual tasks and allow them to concentrate on more interesting, meaningful activities.
Process data mining is proving a big boost to RPA by mitigating certain implementation issues. I learned that it is becoming popular with operational excellence teams who want to identify the best process for using RPA.
But while RPA stands to benefit from process mining, of greater excitement to me at OPEX Week was to discover that process mining might also be a game changer for those of us engaged in process improvement.
Just as data mining helps make sense of massive amounts of data, process mining uses specialized data mining algorithms to let us analyze business processes themselves. And, you guessed it, there can be some real insights and efficiencies to be gained by that.
How It Works
Process mining tools extract process events data from IT systems and then perform analysis of the process data. Each data record must have at least a timestamp, an instance identifier, and some description of what happened to the instance at that particular moment (for example, a status change).
Several open source process mining toolkits exist, and at least 20 vendors make process mining functionality commercially available. At OPEX, I spent some time watching a couple of demos and noticed these useful pieces of screen activity as part of the tools’ output:
Descriptive statistics: The default output is a dashboard revealing stats such as average cycle time, volume, unit cost, and time series.
Process flows with count and time analysis: Here you receive a visual representation of the process flow with the volume of transactions between steps, and average cycle time. This serves as the foundation for value stream analysis and could significantly decrease the time it takes to identify bottlenecks and process inefficiencies!
Bottleneck analysis: With this feature, you are shown a list of events that are creating a bottleneck in the process. When cost data is available and figured into the tool, you can also ascertain the cost of pursuing various paths.
Path analysis: This feature lays out all the different paths in a process. Again, if cost data is factored in, you will be able to see the cost of choosing each path.
Pareto analysis: If dimensional data is loaded, the tools can identify categories having the greatest impact on cycle time. That information is useful in trying to determine where root cause analysis efforts are needed.
Why It Matters
In all of this, two big potential process mining benefits emerge for us process innovators. Number one, process mining could decrease the amount of time it takes to measure and analyze a given process.
To understand this better, let’s go back to our Lean Six Sigma team striving to analyze process data and reduce cycle times on a project. The team works to understand each of the processes in the project minutely. It breaks each process into steps. It figures out the average time that it takes to complete each step. The effort can be laborious.
Process mining changes the picture by doing all of the analysis automatically when you run the process data from your IT system through the process mining software. Your busy executive is no longer waiting months for a solution from your team because you can complete your analysis, theoretically, in a matter of hours.
That is powerful capability to be sure, but the benefit is not just about cutting analysis time—it’s also about the quality of the analysis. Benefit number two of process mining, therefore, lies in its ability to reveal the complexity of existing processes. As I alluded to in my description of the OPEX demos, you can see quite strikingly the different paths that a process might take and readily identify the bottlenecks and processes with the greatest inefficiencies (that is, longer cycle times and variation).
What used to be a manual task for process managers now becomes automatic. And the process mining tool delivers it to you as a forceful visual representation.
Digging Deeper
To my mind, process mining could be a “gold mine” for operational excellence teams. By identifying the best process improvement opportunities while reducing the time needed to conduct the analysis, teams can help their companies reach their continuous improvement goals faster.
Is there a caveat? Yes, there is. Right now, I have largely seen just demos of process mining by its vendors. I’ll need a lot more real-world evidence that process mining can achieve the insights and efficiencies that it promises before I’m ready to dig in.
I’ve returned from OPEX Week charged up and curious to see if process mining will provide, in effect, the business transformation of our profession. What do you think? Have we struck gold with it? Let me know in the comments below. And contact me here on LinkedIn if you would be interested in participating in a Meetup group around the topic of process mining!