3 Building Blocks for Continuous Improvement ft. LEGO
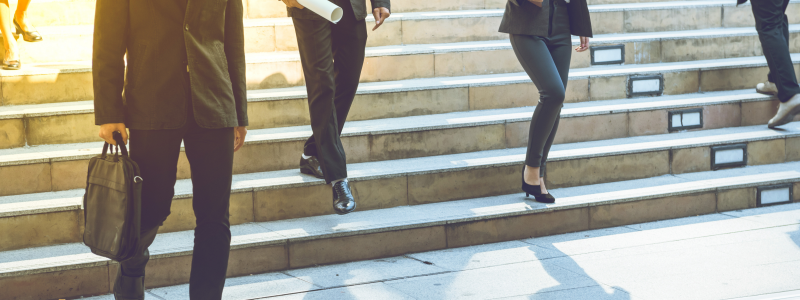
Over the past 15 years, LEGO has achieved what has come to be appreciated as the greatest U-turn in corporate history. In 2004 the Danish-born company was drowning in $800m of debt and was being hit by a 30% loss in sales year-on-year. Despite being arguably the most recognizable toy brand on the planet, 50 years on from it’s inception the plastic brick-maker was struggling to stay afloat in the midst of a rapidly changing market. Verging onto bankruptcy, something had to change.
With the appointment of new CEO Jørgen Vig Knudstorp that same year, LEGO underwent a transformation that radically rebuilt the core business, brick by brick. By 2005, the company had turned its first profit in two years, it quadrupled its return between 2008 and 2010 and in 2015 it announced profits of $660m.
Key to this transformation was the implementation of a culture of continuous improvement that had the strength and longevity to keep up with the company’s unprecedented growth.
On the 9th of October 2019, as the event's chair, Peter Evans, LEGO’s Director of Continuous Improvement in Business Service Operations led a round table to discuss how your business can face up to cultire, improvement and technology at OPEX Europe in Amsterdam, Netherlands. In a recent content piece, we share essential insights from Peter’s 28-years of experience in the change sphere and his personal building blocks for continuous improvement. Here's a snapshot of what the change expert revealed:
1. Understand
For Peter, change occurs at the level of the individual. When transforming the way a business works, change leader must ensure that impacted employees share a mutual and accurate understanding of the end vision and goal. Establishing a formal forum of communication invites an open discussion of what the improvements are, how they’re happening and why and can be of significant benefit in motivating individuals who are adverse to disruption.
2. Improve
When improving processes, intelligent automation is an attractive but costly option. As discovered by LEGO, existing systems and software can be adapted to improve the necessary processes without the additional investment. Always take the time to assess the potential of that which is already in place.
Regardless of whether you do or do not decide to introduce new technology, data plays an integral role in measuring the process of an improvement initiative. Encouraging employees to identify and measure key performance metrics is a great way to keep track of how an initiative is going and build a company-wide improvement mind set.
3. Sustain
A sustained culture of continuous improvement demands the establishment of a core set of values that is both understood and felt by employees. Every action that a business takes should be purposeful and reflect the values that it has outlined. Approaches to hiring and employment alongside interactions with the local community and environment are a great way to put these values into action.
Finally, sharing evidence of the business’ progress with all of those impacted will nurture a culture of improvement that continues to blossom and grow.