Top 10 business transformation teams making a difference
PEX Network presents the 10 business transformation teams that have made an impact in their organizations
Add bookmark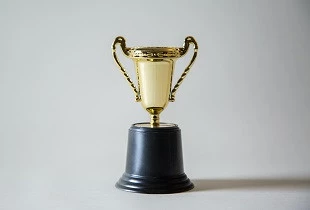
PEX Network is delighted to present its first-ever power list of top business transformation teams that are making a difference in their organizations. PEX Network ran a survey this summer asking you, the process excellence community, to tell us who is having the biggest impact.
The final line-up features teams in many industries including oil and gas, retail, government, manufacturing, sport, telecoms and pharma. Your nominations along with research from PEX Network have informed our list which features teams that have led process improvement breakthroughs and enabled excellence in their organizations.
The PEX Network team would like to thank everybody who took the time to submit a nomination. Of course, there are many more dream teams across the globe who do not feature in this list, which is why our list of the top business transformation teams will return next year – stay tuned.
Pfizer’s DOC Rapid Deployment Program team
Pfizer was already undergoing a digital transformation when the Covid-19 pandemic hit but had to adapt as teams were sent to work remotely. The global pharma company created the Pfizer Global Supply – Digital Operations Center (DOC) project to keep supply continuity for patients and ensure employees remained connected. To accelerate DOC deployment across manufacturing operations within weeks the DOC Rapid Deployment Program was launched.
The DOC provides a shared view of end-to-end manufacturing and operational performance data. Lidia Fonseca, executive vice-president and chief digital and technology officer at the company, explains: “The DOC allows teams to mine data to provide analysis on variations compared to previously estimated standard lead times, enabling further improvement opportunities.”
Related article: Three pharma companies driving operational excellence
The solution helped Pfizer to reduce cycle time by up to 10 percent in some manufacturing areas and it has been key in the production and global rollout of the Pfizer-BioNTech Covid-19 vaccine. The project helped Pfizer win a CIO 100 Award in IT Excellence.
NOV Inc.’s finance team
US-based oilfield equipment company NOV Inc., formerly known as National Oilwell Varco, started its electronic data interchange (EDI) and automation initiative in October 2019. It needed to be able to submit invoices that included more customer requirement delivery options than it already had.
The initiative involved more than 300 people across the organization. The company implemented an artificial intelligence-based e-invoicing solution which helped correct errors in workflow before an invoice was submitted to a customer and pulled requirement information directly from the purchase order.
Read PEX Guide: What is intelligent automation?
Since the go-live in June 2020, the company increased its EDI and automation scope more than 1,000 percent and email automation saved an average of 16 hours per day globally. NOV Inc. implemented a price book matching process which has improved billing accuracy and provides more flexibility for users. Days sales outstanding was reduced by two days overall for automated customers.
Singapore Ministry of Trade and Industry’s BizEngage project team
Businesses that interacted with Singapore’s Ministry of Trade and Industry (MTI) had to provide the same information to multiple agencies on issues, requests and support areas.
The lack of integrated platform and customer relationship management (CRM) capabilities made it difficult for the MTI to drive effective engagement across multiple touchpoints.
Related PEX Network interview: How government agencies can drive OPEX in the public sector
The BizEngage team was created in June 2022 and comprises 30 people across multiple functions and teams in business, operations and tech. The aim was to build a better process to facilitate effective collaboration across multiple different government agencies to deliver a coherent experience for businesses and internal stakeholders.
A CRM platform was implemented which helped MTI achieve a more than 10 percent productivity gain. Sharon Ng, ministry family chief information officer (CIO), says of the initiative: “[We have seen] great collaboration across multiple disciplinary and functional teams, strong industry partnership with a single mission and focus.”
Whirlpool’s North American Manufacturing leadership team
Whirlpool’s North American Manufacturing leadership team won the 2022 Manufacturing Leadership Award for the operational excellence and enterprise integration and technology categories for two distinct projects.
Whirlpool’s Project Tracking System helps assigning project leaders to missions by integrating its experience and workload; it also provides visibility over the root cause of delays. First implemented in the US in 2018, the system now provides visibility to all current and future projects across 14 manufacturing plants in the US and Mexico.
Related PEX Network report: Overcoming inefficient workflows in manufacturing
The Global Kaizen Power Pitch competition took place between May 2021 and January 2022 between and counted 618 participants. A total of 85 “battles” were conducted with 151 Kaizens, or process improvement pitches, presented to cross-functional judging committees. The aim was to recognize plants for delivering manufacturing excellence and motivate employees to achieve excellence. Manufacturing practices that were implemented as a result generated millions of dollars in savings.
Of the two projects, Ramsey Aljahmi, senior director of the North American Region operations excellence at Whirlpool, says: “The Project Tracking System generates significant savings while ensuring seamless delivery of capacity, quality and cost projects across the network. The Global Kaizen Power Pitch completely transformed our ability to share best practices and solutions across all of our global manufacturing plants.”
HP Inc.’s process and digital transformation team
HP’s initiative started in December 2019 with the view to ensure the design of good manual processes before its digitalization. The process and digital transformation team, comprising 14 people, took an Agile scrum approach and joined the receiving operations team and the IT developers.
Read PEX Guide: What is business process management (BPM)?
The process and digital transformation team implemented a digital catalog tool after redesigning the processes around it. It also ensured that the training for receiving operations team contained elements of how the entire process worked, not just how to use the tool.
This approach helped reduce the time for employees to add customer information into the catalog by 30 percent. By understanding the business process behind the forecast process, the team was able to recommend a digital solution to generate weekly forecasts for every sales team around the world. This helped remove 10,000 hours of manual work.
Singapore Pools’ Transformation Program Office
Lottery company Singapore Pools wanted to create a strong delivery framework for its customers, grow innovation and ensure successful internal change management as it automated its manual business processes.
The company implemented robotic process automation (RPA) and initiated a citizen development culture through low-code.
Related PEX Network report: The importance of leveraging low-code to democratize process automation
Through the initiative which involves more than 20 people, the company has achieved more than 82 percent productivity gains with RPA and more than SG$359,000 (US$250,000) in productivity savings. The team has created new pandemic-resistant capabilities that include a remote distributed contact center. It completed an innovation challenge – a hackathon – with eight winning teams whose ideas included charity donation, gamification and self-service capabilities.
Jonathan Lim, head of the company’s transformation program office, states: “[What makes this team successful] is the desire to change, driven by passion and creativity. [We] act on data, define measurables, challenge the norm to make the workplace a great place to work in.”
Red Bull’s Formula 1 pit stop crew
Red Bull’s Formula 1 pit stop crew may be an unconventional addition to this list, but its efficiency has to be noted. Pit stops can make or break a driver’s race and the 23-person pit stop team has to be precise throughout the whole process to hold the driver for as little time as possible.
The process includes the driver stopping at a precise location to avoid readjusting team members’ position. The car is then lifted up onto the jack and wheels are taken out and replaced; there can be a need for cleaning the visor or tweaking the front or rear wing. Then the car is dropped and the driver has to accelerate as soon as the green light hits.
Ahead of the 2019 season, the Red Bull team completed more than 1,200 practice pit stops at its Grove base to ensure consistency across the whole process and maximize ever millisecond. The team won the 2019 DHL Fastest Pit Stop Award for achieving 1.88 seconds with Max Verstappen during the German Grand Prix in 2019. To this day, no other team has beaten them.
Deutsche Telekom’s Deutsche Telekom Services Europe team
Deutsche Telekom’s Deutsche Telekom Services Europe team combines the finance, reporting, procurement and human resources functions. It aimed to digitalize the procure-to-pay process for the entire Deutsche Telekom group, which handles more than two million order items a year. This consists of an annual order volume of more than EUR7bn (US$7bn) and 9 million invoices.
All the core processes in procure-to-pay were already digitalized but the root causes of execution gaps and inefficiencies were not identified. This led to duplicate payments, suboptimal delivery date accuracy that caused penalties, and business decisions made on experiences rather than numbers.
Related PEX Network report: Maximizing business growth through P2P innovation
The team connected data from more than 10 source systems to gain visibility over process flows and create real-time reports. This helped the company achieve a cash discount rate of 96 percent, coupled with additional savings of EUR40mn (US$40mn).
Automation helps the team automatically prioritize invoices to drive on-time payments and achieves this 90 percent of the time. Avoiding duplicate payments has helped the company save EUR3mn (US$2.9mn).
Cumberland Building Society’s operations team
Cumberland Building Society is currently heading into the third year of its five-year Cumberland 2025 Transformation program. The financial services company won the Best Transformation Project Delivering Customer Excellence and the Best Process Transformation Project Under 90 Days awards at OPEX Week: Business Transformation World Summit 2022 which took place in January.
Over the span of 18 months the company created a cross-functional team made of operations and distribution functions to review and improve the end-to-end mortgage application process. Throughout the initiative, 41 employees qualified in Lean Six Sigma.
Related PEX Network report: Enhancing customer experience through a digital mortgage process
The program helped Cumberland Building Society to reduce the cycle time from initial mortgage interview to issuing the offer from 76 to 12 days. It also created a specialist bereavement function to handle such cases more efficiently, which reduced the cycle time from 45 to five days, improving in turn the customer experience.
Schneider Electric’s supply chain team
Schneider Electric was ranked second in the Gartner Supply Chain Top 25 for 2022. The energy management company is in its second year of its supply chain strategy and has accelerated its transformation under its STRIVE pillar: sustainable, trusted, resilient, intelligent, velocity and efficiency.
This award comes after a year of prolonged supply chain disruption as a result of the Covid-19 pandemic. Manufacturers are facing constrained labor availability, global shortages of raw materials and transportation issues.
In light of this, Schneider recognized the need to rethink, reprioritize and reinforce its supplier network and increase local capacity. It implemented a “self-healing” machine-learning supply chain platform with a gal to enhance performance-related parameters that include minimum order quantities, safety stock quantity and lead times in real time. The platform helped the company save more than EUR100mn (US$98.8mn).
What team would you like to include in this list? Let us know by leaving a comment below.