7 ways to manage process variations
How to lose the ball and chain of process variations
Add bookmarkListen to this content
Audio conversion provided by OpenAI
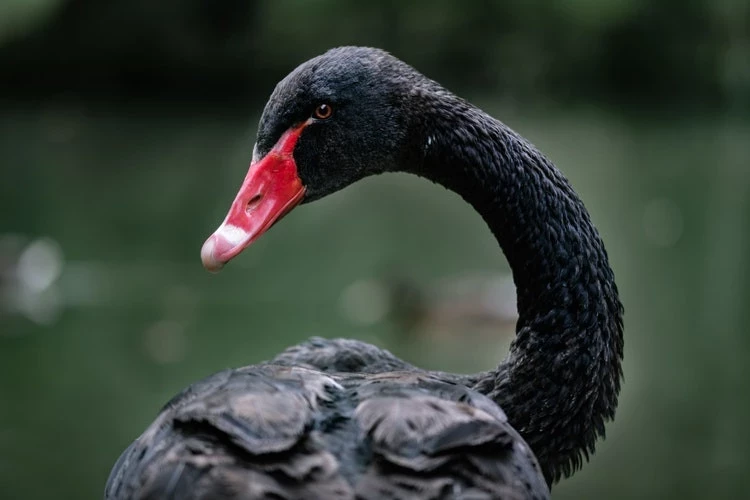
One size fits all. It is an attractive notion for those of us who like the idea of a quick fix. In my experience, however, whether it is a cap, a pair of socks, or a business process – the likelihood of one mould suiting everyone is seldom the case.
For some organizations, business processes vary by geography, by industry, or due to legal requirements. And yet, good business practice dictates that process standardization can increase efficiency, clarify expectations and optimize productivity.
While standardized processes have been proven to save time and minimize errors, sometimes a cookie-cutter approach to the execution of tasks can cause more problems than it solves.
Don't miss any news, updates or insider tips from PEX Network by getting them delivered to your inbox. Sign up to our newsletter and join our community of experts.
Should you expect there to be variations in your processes?
Yes. Increased globalization and advancements in technology see businesses constantly reinventing themselves. With the universal adoption of e-commerce, even the smallest of companies can now do business with customers and vendors in regions that are removed from their headquarters.
Yet those that take advantage of these types of opportunities are required to deal with a range of variables that inherently conflict with process standardization, and can include country-specific product attributes, customer characteristics, regulations and legislations.
To operate effectively despite these challenges, organizations would do well to start by capturing those variations that differ from their core processes — adaptations of the standard processes that take the relevant variables into account, while still aiming for the same outcome.
For example, a U.S. company that produces food products for domestic use as well as for export to Canada will need a standard process that uses the customary system as a weight unit for the U.S. and a process variation that uses the metric system as a weight unit for Canada.
What are the three pitfalls to avoid?
While the need for a flexible approach to managing process variations is obvious, executing on the requirement is often challenging.
Over time I have seen organizations frequently approach process variations in one of the following three ways:
• Create high-level standard processes: Standard processes are defined only at a high level and are not functional as practical guidance. This situation is often found in newly-founded companies.
• Create mega-processes: Often encountered during change initiatives and in technical teams, this scenario involves the meticulous, detailed documenting of every possible process variation. Due to the complexity of the documentation, this system often fails.
• Create individual process variations: In more mature organizations, management often allows this approach, which leads to siloed processes and process sprawl. It compromises the organization’s ability to change and complicates administration.
Clearly, these three methods fail to deliver the efficiency, productivity and visibility organizations are looking to achieve with process standardization.
What are the seven ways to effectively manage process variations?
It is possible for organizations to effectively handle their need for variations outside of their core processes. Here are seven steps to keep in mind:
-
Create a global standard process as a foundation for all variations. With a centralized governance team that consists of global process owners, you can use global processes as benchmarks against which the variations can be measured.
-
Establish local variations where necessary. Local process variations can be created by process variant experts, who must ensure their differences are highlighted against the standard processes.
-
Ensure all process variations are visible. All variations on every process need to be carefully reviewed and compared to standard processes.
-
Make sure teams have easy access to the relevant variations. Leverage a platform that automatically routes teams to those process variations that apply to their business unit, location or other characteristic. Alternatively, provide a list from which they can select the relevant variations.
-
Notify owners of process variations or changes to the standard processes. They can review the changes and either incorporate them into their specific variations or reverse them and keep their variations unchanged.
-
Implement global reporting. Global process owners can review and consequently reject or approve variations.
-
Gather and analyze cost and time data. With this information, you can compare the effectiveness of process variations against standard processes, and determine their efficiency.
Should you let tech do the heavy lifting?
Yes. With the help of a robust process variant management solution, it is possible to manage process variations well. Your software should provide a centralized hub where standard processes are stored and from where variations can be created, and automatic routing points users to the process variations that are most relevant to them.
In addition, a process management platform that has tracking, comparison and reporting capabilities enables you to measure the expense and time associated with process variations. This gives you and your executive decision makers a solid understanding of where you can make improvements and eliminate waste.
As organizations hurtle along the highway of change and globalization, the shortcomings of painting all processes with the same brush become very clear, very quickly. By anticipating and preparing for process variations, business teams can meet operational demands and exceed expectations in an ever-expanding international marketplace.
All Access: AI in PEX is 2025
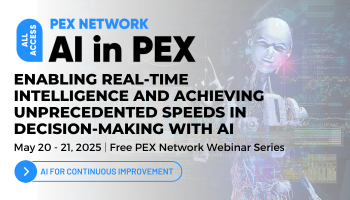
All Access: AI in PEX 2025 is designed to address these challenges and empower organizations to successfully integrate AI into their process improvement initiatives. The content series will bring together industry experts, thought leaders, and practitioners to share insights, best practices, and real-world case studies.
Register Now