"Just Do It" — Problem Solving Made Easy
DMAIC is short for Define, Measure, Analyze, Improve and Control
Add bookmarkListen to this content
Audio conversion provided by OpenAI
At Covance, we expect employees to be process managers, problem solvers, and decision makers. One methodology we in the Six Sigma community use and teach is called DMAIC, short for Define, Measure, Analyze, Improve, and Control.
In the early stages of attempting to instill this methodology within a couple of Covance’s business units, we trained many Green Belts — people who were learning to apply the Six Sigma methodology — to run DMAIC projects that focused on defect reduction.
Don't miss any news, updates or insider tips from PEX Network by getting them delivered to your inbox. Sign up to our newsletter and join our community of experts.
But over the course of time, we recognized some brutal facts:
- Not every defect-reduction challenge required the rigors of the DMAIC methodology.
- The application of the wrong methodology or tools created projects that took too long to complete, which had a negative effect on the perception of the Process Improvement team to be able to solve real business issues quickly.
- Our strategy of embedding the Six Sigma methodology into the culture by giving lean six sigma training to Green Belts only was too exclusive and didn’t allow additional employees to participate.
Facing these brutal facts, we added additional non-Green Belt-specific courses, tools, and methodologies tied to business strategies and needs. We developed a simplified methodology for solving problems that anyone could use. The methodology was designed to tackle problems with obvious solutions or "Just do it" fixes. We called this methodology DPIC, which stands for Define, Plan, Implement, and Control.
DPIC Project Requirements (Define,Plan,Implement, and Control)
|
So, how is this DPIC methodology different from DMAIC? Just as in a traditional DMAIC project, in DPIC we define what the problem is. When the solution is obvious, the employee or employees identify the process problem and bring it to management for approval. If the solution or cause is not known, the employee and his/her manager contact the Process Excellence group. The second phase involves developing a plan to implement the known or desired solution. Once we identify the desired solution, we implement it and control it. At the conclusion of the project, the project leaders contact the Process Excellence group to document the savings, control plans, and celebrate team success.
A DPIC Methodology Case Study
Let us take a look at a specific business example where we chose DPIC over DMAIC as the methodology that would enable us to create sustainable process change in this particular instance.
In June of last year, several leaders from Safety and Quality Assurance (QA) met looking for a way to improve the process of submitting safety reports to QA. These leaders agreed it was possible to use less paper in submissions of reports.
The idea floated around for several months without a directive until one day in August, supervisors and QA auditors revitalized this idea and began working on it. As one team member said, "Let’s explore it, and maybe, just improve it!" So off they went with the blessing of their respective managers. The following describes the steps that the team took to improve the process using the DPIC methodology.
- Define
The team spent some time collecting data from the departments to understand and define the project charter. It was known that the report hand-off processes between Safety and QA consumed a great deal of paper, and the auditing processes were cumbersome and time-consuming. QA auditors and scientists spent hours printing and reviewing copies of the report each time it was submitted. A typical submitted report was printed two to four times before being finalized. For an average 800-page toxicology report, this equated to approximately 24,000 pieces of paper. Over a 12-month period, 422 toxicology reports were completed.
With that number of final reports, the team estimated that the company printed 1,012,800 pages, or 2,026 reams. With reams of pages on the auditors’ desks, the task of reviewing and flipping through pages for content was inefficient and time-consuming. Everyone knew there had to be a better way, but the problem just had not been tackled. - Plan
Armed with the charter and data, the small team began developing their plan by researching current practices at other company sites, mapping their current process, and gathering technical information and input from auditors and report coordinators. They created process maps and collected the Voice of the Customer from the process stakeholders
Along the way, they recognized a second opportunity for improvement regarding the resubmission process. The resubmission processes were inefficient and consumed large quantities of time. Baseline data indicated that auditors were spending on average 10.9 hours auditing re-submission reports — once again, comparing the cumbersome paper copies for changes.
The team knew it made sense to fix both problems simultaneously. They met two to three times a week for six weeks; during this time they brainstormed solutions, mapped new processes, tested possible solutions, and worked around the technological and financial barriers. They used the Voice of the Customer data and process maps to create a future state process that would be implemented to meet their stakeholder requirements. Once they had a working model for the new process, they devised a plan for implementation, which included a training plan, a communication plan, and a scorecard. The team got approval and went to work on implementing the approved solution. - Implementation and Control
In late September, a plan was complete and the process was rolled out to the departments. The team met with QA and Safety leadership to present a new process — electronic submission! Two training programs were developed and delivered, and the new process was launched in mid-October. They expected to radically reduce paper usage and QA auditor re-submission time. The scorecard was maintained by the department leadership, and data collection was in place to measure effectiveness.
With minor corrections, all aspects of the process were in place by mid-November. The improvement effort fit within the DPIC methodology requirements. The team reduced the amount of paper used in these processes by 95 percent, saving 122 trees per year and reducing by 30 percent the labor hours for re-submitted reports.
The new process addressed both paper use and auditor efficiency for both initial reports and subsequent submissions. This is just one example of a successful DPIC project that was completed at Covance. - Producing Results
Our results following the roll out of the DPIC methodology have been positive. The number of improvement projects has more than tripled, and more employees feel empowered to make changes within their areas.
PEX Report 2024 global state of process excellence
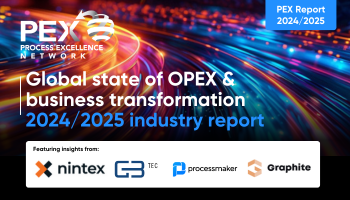
PEX Network's annual report reveals the current state and future trends of process excellence. Based on a study profiling hundreds of global process excellence leaders, the report provides insights on how to leverage innovation, generative AI, and process intelligence to achieve operational excellence, customer-centricity, and organizational growth. Download your copy of the PEX Report 2024/2025 today and benchmark your process excellence journey against your peers.
Download Now