Prevent recurring defects with root cause analysis
Find out what root cause analysis is and why it's critical
Add bookmark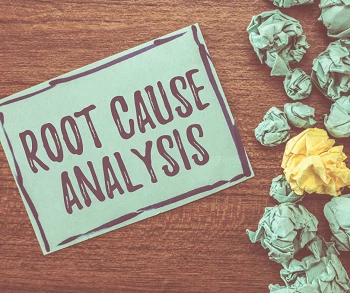
Quality is equivalent to the ratio of good parts to total parts. A defect is a criterion that makes a part non-conforming. The defect type could be dimensional, visual, cosmetic, performance-oriented, etc.
Root cause analysis is the method in which the reason for the cause of the defect is evaluated and identified so as to identify the containment, corrective and preventive action, which will contribute to the prevention of the defect’s recurrence.
This process is extremely critical because if the correct root cause is not identified, then the defect impacts quality again and again and again. Recurrence of defects is bad for efficiency, productivity and employee morale.
Don't miss any news, updates or insider tips from PEX Network by getting them delivered to your inbox. Sign up to our newsletter and join our community of experts.
Types of root causes
More often than not the root cause will fall under one of the variables below:
Dimensional: The part dimensions may not conform to the specifications of the customer. It could be outside the tolerance limits specified by the customer, and this may impact functionality of the final part.
Process oriented: There are many input variables in a process, like speeds, pressures, temperatures, etc. Defects in a final product may be as a result of the input variables falling outside the window of "what works" assembly techniques.
Visual/cosmetic: Functionality is extremely critical but there are almost always aesthetic requirement for a product. As an example, if you are in the market for a LCD TV, even though it may completely conform functionally, if the frame of the TV is not clean, shiny or fails to look like new, the customer will choose an alternate piece of the same product specifications.
Material properties: The physical properties of the raw material used to make a final product may fall outside the specifications, which may lead to defects in the parts. For example in the case of metal commodities, hardness value spec, tensile strength, etc...
Environmental: Environmental is to describe the conditions like temperature, pressure and conditions in which the process operates. In this scenario, it may be possible that there are multiples causes that have an aggregate in terms of the impact on a defect.
How do you diagnose the root cause and how do you validate the root cause?
A root cause diagnosis can be done with the use of various tools like 5 Whys, fault tree analysis, Ishikawa (fish-bone) diagram, cause and effect diagram, etc., so on and so forth. The root cause is done by evaluating the inputs, process and the impact on the output.
Root cause analysis framework
The framework used in root cause analysis is done with the following steps:
Contain: This step may even be conducted in parallel to the define step described above. Time is money, and every second the problem is not contained dollars are wasted. The CONTAIN step is the band aid to stop the bleeding. This step will probably include the following sub steps like:
- Identify the timeframe when the defect is estimated to have happened and quarantine the stock.
- Send out an alert to all who need to know.
- Define sorting criteria and start sorting good and bad stock.
- Is there a temporary rework that can be implemented?
- Who needs to perform the temporary rework if it can be done.
Define in detail: As the name suggests, the more details the better. One of the most efficient ways of doing this is to have a "good" part photo alongside a "bad" part photo highlighting the defective side of the part. A brief 3-5 line description of what is "bad" and what the impact of the defect is extremely critical.
Analyze: This is the part where we dive in and try to understand what caused the defect. The questions that are answered are:
What caused the defect?
- Inputs /Process/Environment
Based on the defect it may be possible to narrow down the variables that have contributed to it. At the same time it is also important not to ignore some of the potential variables. More often then not the process owners and users have a fairly good understanding. - The variables identified need to be subjected to Why? Why? Why? Why? Why? (I do not like to limit myself to 5 Whys; I try to keep going until I cannot go any further so it may be 2 Whys and it may be 7 Whys in other instances.)
- Validate the identified root cause with data (hint: by replicating failure)
Why did the current manufacturing process not prevent the defect?
Is this a new issue?
Was the defect identified in the planning/design process?
If this is a known issue
- Was there a previous short term and long term action identified?
Why did the previous fix not prevent this defect?
Why was the defect not contained if it was a known issue?
Improve and prevent: At this stage the root cause has been identified and validated. It is time to design and implement a solution.
The critical points of this activity:
Improve
If this is a recurring issue, it is important to understand why the solution implemented failed to prevent the defect from reoccurring.
If it is a new issue, the root cause will drive the improvement action.
Retraining or firing the operator or adding a visual inspection is not a valid permanent fix. The goal of the improvement action/s is to prevent the defect from surfacing again.
Prevent
It is important to include this step in the process FMEA (Failure Mode and Effects Analysis). This will support the prevention of the recurrence of the defect. The Process FMEA is a "live" document and must be reevaluated at a fixed time interval or when there are design/process changes.
How process intelligence transforms manufacturing & supply chains: 2025 industry report
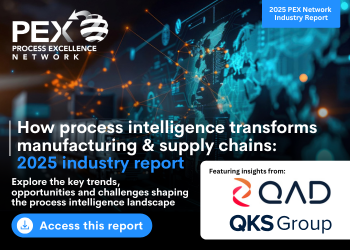
This industry report examines how and why organizations are investing in process intelligence to enhance manufacturing and supply chain management. “Global manufacturing and supply chains face enormous volatility in 2025,” says Michael Ochi, director at QAD. “Individual organizations feel tremendous pressure but also have new opportunities to grow. Any combination of protective and expansive business strategies requires constant speed and awareness.”
Organizations with significant manufacturing and supply chain operations are turning to process intelligence because it is uniquely capable of providing speed and awareness to any part of the business that leverages software.
Download the report to explore:
- The top five trends shaping process intelligence.
- Case study examples of process intelligence transforming manufacturing and supply chains.
- The key success factors and challenges of process intelligence adoption