8 Wastes of Lean Manufacturing in a Services Context
Add bookmarkListen to this content
Audio conversion provided by OpenAI
Defining "Waste" As it Applies to Service Organizations
Anything that does not add value to the customer is a waste. Waste only adds to time and cost.And the definition of "waste" in a service organization is quite similar to its Lean manufacturing definition.
When you look at a process, this customer could be an external customer/end user (consumer) for a process that has an impact on customers. For an internal process of an organization, this refers to an internal customer. Examples of the process of the former types include: sales, marketing, production, etc. The examples of the process in the later bucket include training, recruitment, administration, etc.
Don't miss any news, updates or insider tips from PEX Network by getting them delivered to your inbox. Sign up to our newsletter and join our community of experts.
The 8 Wastes of Lean Manufacturing
Kudos to Taichi Ohno, the father of Toyota Production System. His 8 wastes of Lean manufacturing have a universal application. Despite what some practitioners may say or write, the 8 wastes of Lean are applicable not just in a Lean manufacturing system but also in services. Take any context and you'll see for yourself the applicability of the wastes as expressed by Ohno.
Table 1 summarizes the 8 wastes of Lean with examples from services. I have kept a column empty for you to fill with the ones that are visible in your own company.
Type of waste |
What is it? |
Examples |
Waste of Over-production |
Processing too soon or too much than required |
• Information sent automatically even when not required |
Waste of Defects |
Errors, mistakes |
• Rejections in sourcing applications |
Waste of Inventory |
Holding inventory (material and information) more than required |
• Files and documents awaiting to be processed |
Waste of Over-Processing |
Processing more than required wherein a simple approach would have done |
• Too much paperwork for a mortgage loan |
Waste of Transportation |
Movement of items more than required resulting in wasted efforts and energy and adding to cost |
• Movement of files and documents from one location to another |
Waste of Waiting |
Employees and customers waiting |
• Customers waiting to be served by a contact center |
Waste of Motion |
Movement of people that does not add value |
• Looking for data and information |
Waste of Un-utilized People |
Employees not leveraged to their own potential |
• Limited authority and responsibility |
Waste of Over-production |
Processing too soon or too much than required |
• Information sent automatically even when not required |
Waste of Defects |
Errors, mistakes |
• Rejections in sourcing applications |
Table 1 — 8 Wastes of Lean Manufacturing with Examples From Service Organizations
In Conclusion of the 8 Wastes of Lean Manufacturing
The above definition of the 8 wastes of Lean should be looked at as something that is directional and should always be kept in mind while taking up a Lean optimization project. These are also called Non-Value Added activities, and I have seen processes in service business wherein up to 95 percent of the time is spent on these Non-Value Added activities. I shall talk about the concept of Value Added/Non-Value Added/Business-Value Added activities in my next column. Understanding this concept is a must for dissecting a process for Lean transformation.
Appreciating waste in a service business can be quite challenging as many of the activities do not happen before one’s eyes. What is needed is the usage of value stream mapping, which helps bring out the tacit wastes in a process. This has to be supported with sharp judgment of the change agents that are catalyzing the process improvements.
The 26th Annual OPEX Week: Business Transformation World Summit | post show report
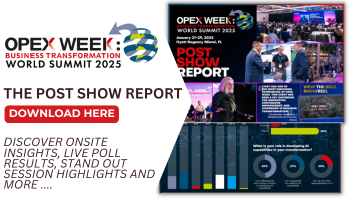
Over 550 transformation leaders from 200 companies across 17 countries gathered to share innovations and stories at OPEX Week 2025. The three unforgettable days sparked groundbreaking ideas and invaluable connections. Don't worry—we've got you covered with a full recap of the 2025 OPEX Week. Download the post-show report here.
To view this content, please fill out the form to register and become a member.
Or, if you're already a member, sign in below to view.
Please note: That all fields marked with an asterisk (*) are required.