The Check Sheet: A Simple and Effective Way to Display Data
Add bookmarkListen to this content
Audio conversion provided by OpenAI
The check sheet is another simple and effective tool useful in Lean Six Sigma projects. It is sometimes referred to as a concentration diagram or location plot. It is a handy tool for both qualitative and quantitative data gathering and analysis. Check sheets help to systematically collect and organize data and is useful in the all phases of the Lean Six Sigma DMAIC (define, measure, analyze, improve and control) framework.
Don't miss any news, updates or insider tips from PEX Network by getting them delivered to your inbox. Sign up to our newsletter and join our community of experts.
Check sheet vs. check list: People sometimes confuse a check sheet with a check list. The list we use for groceries and the report you get from the auto repair shop with things checked off after service (oil, filter, tire pressure, tread, etc.) are examples of a check list. The following table highlights some key differences between a check list and a check sheet.
Check Sheet | Check List |
A tally sheet to collect data on frequency of occurrence | A tool used to ensure all important steps or actions have been taken |
Custom designed by user | Often a standard form is used |
One of seven quality tools | Not one of the seven quality tools |
E.g.: Check sheet to document reasons for interruptions in OR | E.g.: All items in case cart are present before surgery in OR |
When to use the check sheet: Using a check sheet is appropriate when the data can be observed and collected repeatedly by either the same person or the same location. It is also an effective tool when collecting data on frequency and identifying patterns of events, problems, defects, and defect location, and for identifying defect causes.
Types of check sheets: Commonly used check sheets are tabular check sheets or tally sheets, location check sheets and graphical or distribution check sheets.
When to use the check sheet: Using a check sheet is appropriate when the data can be observed and collected repeatedly by either the same person or the same location. It is also an effective tool when collecting data on frequency and identifying patterns of events, problems, defects, and defect location, and for identifying defect causes.
Tabular check sheet or tally sheet: The tally sheet is commonly used to collect data on quality problems and to determine the frequency of events. For example, the tally sheet is useful for understanding the reasons patients are arriving late for appointments, causes for delays in getting the lab results back, etc. It is also useful in determining frequency of occurrence, such as number of people in the line for blood tests at 6:00 am, 6:15 am, etc., to understand staffing needs.
Location or concentration diagram: When you rent a car, you probably receive a document with the sketch of the car which allows you to circle any damages, dents or scratches on the car with a corresponding mark on the diagram. This is an example of the location diagram. (Click on image to enlarge.)
A variation of this could be to mark directly on the form where mistake occurs. For example, if information is missing on an application, you could mark it directly on the form.
Don't miss any news, updates or insider tips from PEX Network by getting them delivered to your inbox. Sign up to our newsletter and join our community of experts.
Graphical or Distribution check sheet: Using the graphical form, the person collecting the data is able to visualize the distribution of the data. For example, the number of people in line at the registration desk at 15 minute intervals could be counted to determine the staffing needs and the size of the waiting room. (Click on image to enlarge.)
Advantages of using the check sheet: The check sheet is a simple and effective way to display data. It is a good first step in understanding the nature of the problem as it provides a uniform data collection tool. It is very useful to help distinguish opinions from facts in the Define and Measure phase of the Lean Six Sigma DMAIC framework.
Some examples: In our discussions for reasons for retained foreign objects, the Lean Six Sigma team kept hearing about the frequent interruptions in the operating room, but was unable to quantify the magnitude of the problem. We developed a check list to quantify the interruptions and distractions in the operating room and piloted the form for four weeks; the data helped the team quantify pagers as one of the leading causes of interruptions in the operating room. The hand hygiene check sheet piloted by the Lean Six Sigma team is another tool that helped to standardize hand hygiene compliance at Mayo Clinic. View the hand hygiene check sheet here.
PEX Report 2024 global state of process excellence
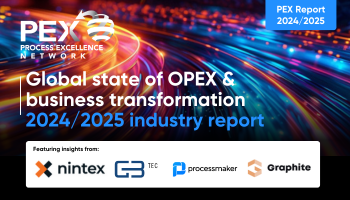
PEX Network's annual report reveals the current state and future trends of process excellence. Based on a study profiling hundreds of global process excellence leaders, the report provides insights on how to leverage innovation, generative AI, and process intelligence to achieve operational excellence, customer-centricity, and organizational growth. Download your copy of the PEX Report 2024/2025 today and benchmark your process excellence journey against your peers.
Download Now