Why the real value of process mining lies in simulation
Frances Sneddon, CTO at Simul8, explains why combining process mining and simulation offers a predictive edge for businesses
Add bookmark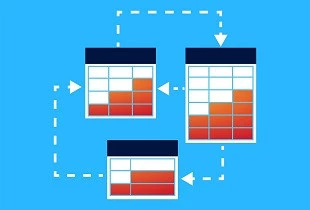
Gartner refers to process mining as “the art of discovering, monitoring and improving processes to increase operational resilience”. It is a tried and tested methodology embraced by enterprise architects and innovation leaders around the world, but is it being leveraged to its fullest potential?
While process mining can be used to define parameters such as caseloads, execution times, idle resources and process flows, only simulation can put these parameters to work and build hypothetical models that reveal the true 360-degree impact of even the smallest decision. In a world where the efficiency of a business is based on rapid, often reactive decision-making, only simulation modeling holds the key to unlocking true continuous improvement.
In this article, we explore the relatively untapped potential of continuous improvement, why process mining and simulation modeling go hand-in-hand and why businesses in 2021 need to start looking beyond conformance in order to reach their true potential. First, let us take a brief look at process mining.
What are the three components of effective process mining?
There are three typical components that make up effective process mining. The majority of businesses lean on process mining as a tool of discovery, highlighting inefficiencies and gaps in productivity which they can then go and fix.
Businesses that want to take this one step further will use process mining for conformance, which involves benchmarking current processes against a set of desired functions, usually in the interests of meeting compliance and regulatory objectives. Then there is enhancement, which is about making those changes and fulfilling those objectives.
For many organizations, however, this is where the process mining conversation seems to end. According to a report by Gartner, one in four businesses actively use process mining together with simulation modeling to achieve continuous improvement, a near-constant transformation strategy which keeps businesses in their most lean and productive states.
The powerful combination of process mining and simulation modeling
There has been a pivotal shift in attitudes toward productivity and the role of real-time data. Instead of thinking about process mining as a project with a fixed beginning and end, businesses are starting to see the advantages that lie in a fully integrated, business-wide improvement strategy with changes measured in hours, rather than in weeks or months.
These benefits extend far beyond Industry 4.0, from retailers optimizing warehouse and distribution functions, to hospitals streamlining their flow of patients. What is the missing piece of the puzzle? Modeling and simulation.
Process mining and the principles of discovery, conformance and enhancement are traditionally based on historical 'static' data. It is useful and adaptable, but it is dependent on event data from existing processes, which limits its usefulness beyond conformance and one-off enhancements.
Historical event data is no doubt essential, but rather than using it purely for conformance checking, organizations can use the mined data as the basis for future simulation models. If artificial intelligence (AI) and machine learning (ML) were seen as useful in the discovery and conformance phases of process mining, they are going to be invaluable in the modeling and simulation of future scenarios, as businesses turn their attention to continuous improvement.
Process modeling, therefore, moves the focus away from mere diagnostics and onto more modern, forward-thinking optimization. Rather than assessing the impact of what one small-scale change might make to one department or production line, businesses can instead leverage the power of simulation to see the effects of that change in the round. This lends businesses a powerful predictive edge in their pursuit of operational productivity that might otherwise be unavailable, helping them to tighten up productivity and ROI.
Take triage and the distribution of healthcare during the Covid-19 pandemic for instance. With patient numbers rising exponentially, healthcare providers needed to prioritize the most severe cases, ensuring the correct number of beds, equipment and staff would be on hand to meet capacity.
While process mining and conformance may allow hospitals to function optimally during normal times, weeding out inefficiencies and complying with regulations, only digital simulation could offer the insight and foresight to deal with the unprecedented circumstances of the pandemic. With simulation technology, healthcare workers can take mined data one step further, allowing them to make snap decisions on how to deploy resources in the most effective possible way.
The call center is another environment that has been caught off-guard by the fallout from the pandemic. With retailers and service-providers temporarily losing their presence on the high street, online and call center channels have come under increased pressure. That pressure is compounded by a general shift toward omnichannel customer service, with customers now expecting a more seamless non-linear experience between online chat, call centers and website activity.
A great deal of work has been done over the years to determine what constitutes optimum operational efficiency in call centers including call capacity and staffing requirements. These nonlinear customer journeys, combined with the ‘randomness’ of call center use since the pandemic began, has rendered frameworks such as the Erlang formula obsolete.
Again, data mining and digital simulation can provide the key to adapting to these variables and more, making the unpredictable easier to navigate. Not only can simulation help call centers optimize for volume and capacity, but it can also enhance staff experience, firefighting during peak times and management of complex cases.
The applications of combining process mining and process modeling with a simulation overlay are only just starting to be realized by a handful of sectors, but the potential knows no bounds. Soon, focus will move away from structured process automation tools such as RPA in the pursuit of conformance, and onto the application of AI, ML and neural networking in event simulation and modeling, all in the interests of ongoing, continuous improvement.