Intelligent automation is reshaping the food distribution industry
Gordon Food Service’s Deji Adedayo discusses how the food distribution company uses intelligent automation to enhance operations
Add bookmark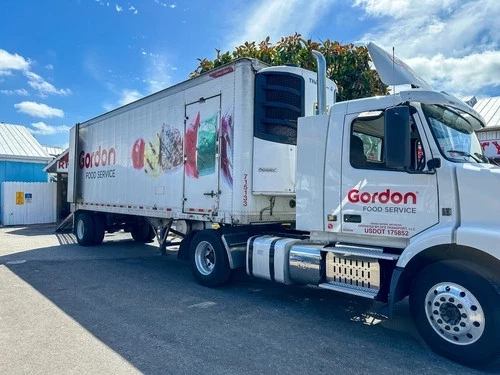
Intelligent automation (IA) combines artificial intelligence (AI), robotic process automation (RPA) and business process management (BPM) to help organizations streamline tasks, improve efficiency and cut costs. It’s one of the hottest topics in the modern business landscape right now, using large data volumes, precise calculations, analysis and business implementation to simplify processes, free up resources and improve operational performance.
Deji Adedayo is IA lead and product owner (North America) at Gordon Food Service (GFS). GFS is the largest family-operated broad-line food distribution company in North America, serving the Midwest, Northeast, Southeast and Southwest regions of the US and coast-to-coast in Canada.
Adedayo has spearheaded numerous transformative projects across various industries, demonstrating a unique blend of technical acumen and strategic insight with a commitment to optimizing processes and enhancing efficiency. He is speaking at All Access: Intelligent Automation 2024 (June 18-19), the next installment in PEX Network’s free webinar series, where he’ll be discussing overcoming automation silos for unified success.
Ahead of the event, we spoke with Adedayo to explore how GFS applies IA and its impact on the food distribution industry.
Don't miss any news, updates or insider tips from PEX Network by getting them delivered to your inbox. Sign up to our newsletter and join our community of experts.
PEX Network: How does GFS use IA to enhance operations?
Deji Adedayo: I remember a couple of years back when I started at GFS, the IA program was very new. Fast forward to a few years after, IA is increasingly being leveraged to enhance operations across several key areas. The same can be said for the entire food distribution industry. Here’s how IA is applied:
- Finance: IA has been leveraged for automated invoicing and payments, financial forecasting and planning, expense management and optimization, regulatory compliance and fraud detection. It is helping to reduce human keying errors, accelerating billing process and ensuring accuracy. It also reduces the workload of finance teams, decreases the risk of payment errors and reduces risk of fines and legal issues.
- Supply chain optimization: IA has been leveraged to automate inventory management and demand forecasting, helping in maintaining optimal inventory levels, limiting waste due to spoilage and reduces risk of overstocking or stock outs.
- Logistics and distribution: IA tools are helping to analyze delivery routes and traffic data in real time to optimize schedules and speed up delivery time. IA is also helping with preventive maintenance – shortening time to inspect equipment and trucks.
- Operational efficiency: Automating repetitive and rule-based tasks such data entry into SAP and other ERP systems, reducing time spent on administrative tasks and minimizes the likelihood of errors.
IA is also helping to improve customer satisfaction, adhere to compliance standards and drive growth.
READ: Intelligent automation in 2024: Trends, benefits and use cases
PEX Network: What benefits does IA offer your organization?
DA: IA has offered a range of significant benefits and advantages across various operational dimensions, including:
- Increased efficiency and productivity: IA technologies like RPA have helped optimize workflows, automate repetitive and time-consuming tasks and reduce the time and effort required to complete processes/tasks. We have saved thousands of hours of annual time spent performing mundane and administrative tasks.
- Operational cost reduction: IA has helped optimize resource utilization, reducing waste and minimizing errors, which in turn cuts down operational costs.
- Enhanced decision-making: IA has enhanced decision-making by providing new and actionable insights into processes, helping managers make better, informed decisions.
- Direct impacts to bottom line: IA technologies are helping in identifying and submitting claims to vendors for refunds, bringing back thousands of dollars.
Incorporating IA has not only helped in streamlining processes and operations, but provided that competitive edge needed by enhancing capabilities and improving service delivery.
READ: 6 things intelligent automation can’t do for your business
PEX Network: What are the biggest IA challenges and why?
DA: The challenges include:
- Integration complexity: Companies in the Food distribution industry have legacy systems and integrating IA with these systems can be complex because they often lack the necessary flexibility or functionality to seamlessly integrate with new technologies. Furthermore, varying requirements may not be easily compatible with existing IT infrastructure.
- Cultural resistance: Resistance to change for fear of job displacement or distrust in the reliability of automated systems is very common. Getting buy-in from all levels of an organization can be difficult, particularly if the benefits and uses of IA are not well understood. These can prevent growth and idea generation.
- ROI calculation and project-specific benefits: Calculating ROI, defining project-specific benefits and tracking benefits are significant challenges.
- Automation silos: Silos pose a significant challenge to effective implementation and scalability of IA. Implementing fragmented, department-specific IA without a cohesive, organization-wide strategy often leads to scalability issues.
READ: 6 free intelligent automation training courses for business leaders
PEX Network: How will IA shape the future of the food distribution industry?
DA: In a very competitive food distribution industry, IA will significantly shape the future of food distribution by:
- Enhancing supply chain efficiency: IA can optimize the entire supply chain, from forecasting demand and managing inventory to logistics and delivery. Automated systems will predict demand with high accuracy, adjust inventory levels in real time and optimize delivery routes to reduce costs and delivery times.
- Improved customer service: AI-driven chatbots and virtual assistants that can handle customer inquiries and orders around the clock will offer more personalized and responsive customer service, providing immediate responses and updates on order status, delivery date and time and product availability.
- Data-driven decision making: IA tools can collect and analyze data from various points in various areas, generating new insights into customer preferences, behaviors, market trends, operational bottlenecks, reduce fuel consumption and cost on parts and equipment for transportation.
The 26th Annual OPEX Week: Business Transformation World Summit | post show report
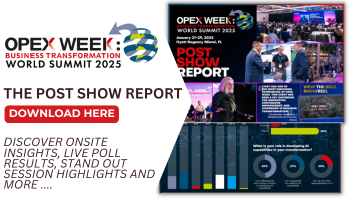
Over 550 transformation leaders from 200 companies across 17 countries gathered to share innovations and stories at OPEX Week 2025. The three unforgettable days sparked groundbreaking ideas and invaluable connections. Don't worry—we've got you covered with a full recap of the 2025 OPEX Week. Download the post-show report here.
To view this content, please fill out the form to register and become a member.
Or, if you're already a member, sign in below to view.
Please note: That all fields marked with an asterisk (*) are required.