UK manufacturing sector recovers but are AI & energy priorities misaligned?
UK manufacturing bounces back to growth amid surging production levels and business optimism
Add bookmark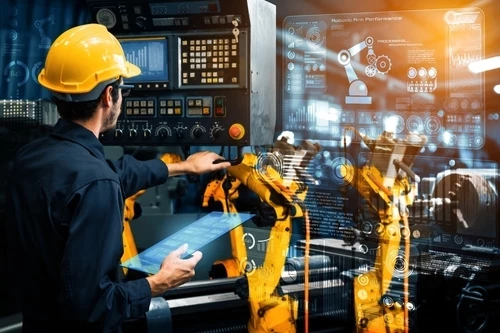
The UK’s manufacturing sector saw significant growth in May as levels of production surged amid growing business optimism. The S&P Global/CIPS UK manufacturing PMI survey rose to 51.2 in May, after falling back to 49.1 in the previous month. Any reading above 50 means a sector is in growth, while a score below this means it is contracting. Production expanded at the quickest rate since April 2022, with consumer, intermediate and investment goods registering expansions. However, research and thought leaders warn of misalignment of the UK manufacturing sector’s priorities moving forward.
A report from Mitsubishi Electric revealed a disconnect in relation to the sector’s actions to address energy price volatility. Energy on an Industrial Scale surveyed 200 senior decision-makers working in UK manufacturing about how the sector can increase its overall resilience. It found that 91 percent of respondents expressed concern over energy price security and 85 percent were worried about grid resilience.
“This report provides a much-needed snapshot of the manufacturing sector’s most pressing challenges, and underlines why decision-makers can no longer delay action,” comments David Bean, business development group manager at Mitsubishi Electric Automation Systems UK. “However, the pressures and instability affecting the industry may have made businesses reluctant to do so.”
Don't miss any news, updates or insider tips from PEX Network by getting them delivered to your inbox. Sign up to our newsletter and join our community of experts.
Likewise, while autonomous/robotic technology has undoubtedly revolutionized the manufacturing industry driving efficiency and productivity, overreliance on machines can be extremely dangerous, warns Marc Wren, OT cyber security manager Axians UK.
“Manufacturers are increasingly leveraging the capabilities of artificial intelligence (AI) and machine learning to achieve new levels of efficiency and production control.” Autonomous planning is a use of AI that is being rapidly adopted across the manufacturing industry. AI algorithms analyze real-time data on inventory levels, production capacity and customer demand as well allowing manufacturers to maintain a consistent supply performance by analyzing historical data on material usage, lead times and potential disruptions. “Machines, for all their processing power, lack the critical thinking and problem-solving skills of humans,” adds Wren.
READ: 8 wastes of Lean manufacturing in a services context
Human-machine collaboration
“As the manufacturing sector evolves, it faces a pivotal moment in determining priorities for the future,” says Wren. “The arrival of Industry 5.0 marked a significant shift, underscoring the indispensable role of human ingenuity alongside cutting-edge technology. This paradigm shift calls for manufacturers to embrace a collaborative approach, integrating human skills with machine precision to drive innovation and resilience.”
Manufacturers who prioritize Industry 5.0 understand that the true competitive edge lies in collaboration, not replacement. Machines cannot always recognize obstacles, and although robots excel at repetitive tasks, they lack the situational awareness crucial for safe human-machine interaction. “At the end of 2023 a Tesla engineer was severely injured by a robot, he was only freed from the machine’s grip because a colleague pressed the emergency stop button. The incident demonstrates the vulnerability of relying solely on machines,” says Wren.
If a machine on the assembly line malfunctions, a fully automated system might grind to a halt. However, a human-machine partnership will flourish. “Imagine a chemical factory malfunction – a computer might not understand the situation or act quickly enough to prevent a spill. In this scenario, a human can assess the problem, override the system if necessary, and take actions to prevent a disaster,” says Wren.
A skilled technician, equipped with real-time data and insights from the machine itself, can quickly diagnose a problem and implement a solution. This not only minimizes downtime but also fosters a deeper understanding of the machinery, potentially preventing future occurrences. “This exemplifies the power of Industry 5.0, combining human rationale with machine precision for optimal results,” Wren adds.
READ: 6 things intelligent automation can’t do for your business
Balancing cost, capacity and energy use
Capacity, cost, carbon reduction and resilience are four key drivers for manufacturers today, each having a major impact on how, when and why a site operates. Striking a balance between these points can be difficult, especially as the energy market is subject to volatility and unforeseen change. This makes it critical to adopt the right tools.
The Mitsubishi Electric report paints a clear picture of decarbonization pressures. While 85 percent of respondents said working towards net zero was a key part of their business with 70 percent stating they had been asked to report on scope 1/2/3 emissions for a tender process, only 35 percent were currently implementing net zero within their operations. What’s more, only 24 percent of those questioned have a fully implemented on-site energy management system and just 27 percent employ a dedicated energy manager.
READ: Why AI isn’t a green technology for data operations
“These statistics are not only eye-opening at face value, they need to be considered within the context of how energy pricing has changed in the past few years,” says Bean. “The sector is just coming out of one of the worst energy crises in modern memory, and the impact of this price volatility is yet to be fully felt.”
Bean advocates manufacturers to understand their goal and take small but necessary steps with a tangible ROI in order to achieve an energy strategy based on digitalization to improve decarbonization, energy resilience and carbon footprint. “By starting small and implementing new tools and technologies including energy management systems, site teams, senior managers can access meaningful data needed to make these necessary decisions. It doesn’t matter where you are on your energy journey, we can help businesses develop a roadmap to a greener and more resilient future.”
All Access: AI in PEX is 2025
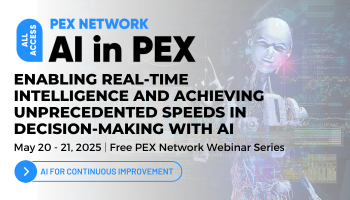
All Access: AI in PEX 2025 is designed to address these challenges and empower organizations to successfully integrate AI into their process improvement initiatives. The content series will bring together industry experts, thought leaders, and practitioners to share insights, best practices, and real-world case studies.
Register Now