Deficit in skills needed for digital transformation & NHS uses Celonis' SE process mining platform
There is a dramatic deficit in skills needed for digital transformation, and NHS fixes bottlenecks with Celonis' process mining tech
Add bookmarkListen to this content
Audio conversion provided by OpenAI
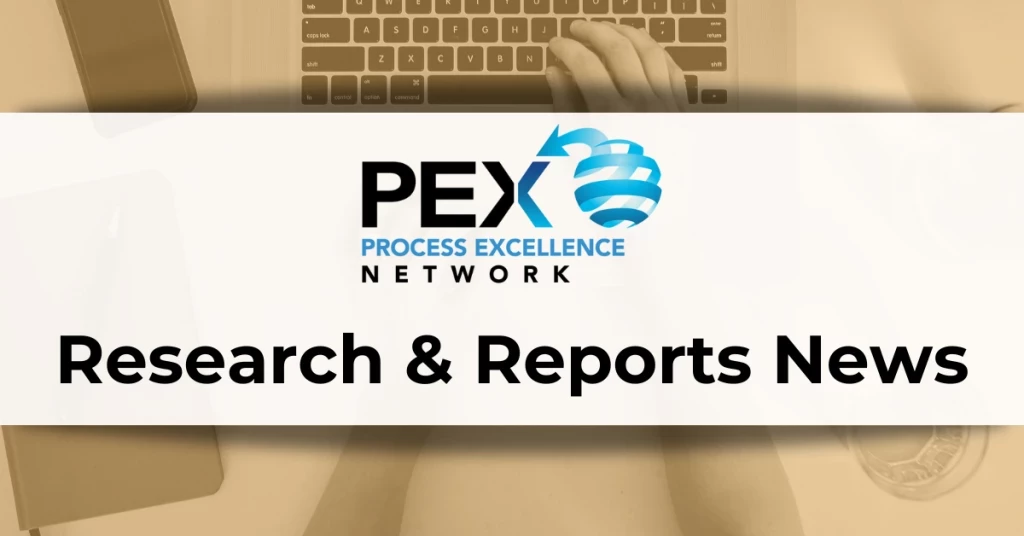
PEX Network’s weekly news bulletin rounds up the latest research, reports and publications in operational excellence (OPEX), digital transformation, artificial intelligence (AI) and automation, business process management (BPM), process mining and process intelligence and more.
This week includes:
- Study reveals how low-tech firms drive transformation through business model reconfiguration
- NHS fixes healthcare bottlenecks with Celonis' SE process mining platform
- “Dramatic” deficit in skills needed for digital transformation
Don't miss any news, updates or insider tips from PEX Network by getting them delivered to your inbox. Sign up to our newsletter and join our community of experts.
Study reveals how low-tech firms drive transformation through business model reconfiguration
A recent study in the Business Process Management Journal sheds light on how small, low-tech firms can achieve business transformation through business model (BM) reconfiguration. Researchers Aruana Rosa Souza, Kadigia Faccin, and Caroline Kretschmer conducted an in-depth case study on a traditional low-tech company, showing how it adapted to external changes by strategically realigning key components such as resources, partnerships, and organizational structures.
The study reveals several crucial factors that enabled the firm to reconfigure its business model:
1. Leveraging strategic partnerships:
Partnerships were vital in providing the company with access to additional resources, networks, and expertise, which supported adaptive strategies. Collaborating externally enabled the firm to accelerate its response to industry pressures without requiring heavy investment in new technologies.
2. Emphasis on organizational flexibility:
Organizational flexibility allowed the firm to pivot in response to market demands. Low-tech firms were shown to benefit significantly from adopting less rigid structures, enabling rapid adjustments to both challenges and opportunities.
3. Prioritizing core resources:
Instead of pursuing high-tech innovations, the company focused on optimizing and reallocating its existing resources. This approach allowed it to remain relevant, adapt to customer needs, and maintain a competitive edge within a low-tech market environment.
The researchers recommend that managers of small, low-tech firms adopt a reconfiguration mindset to drive transformation.
NHS fixes healthcare bottlenecks with Celonis' SE process mining platform
The NHS has tapped into the potential of Celonis SE’s process mining platform to help untangle healthcare bottlenecks across its network. Daniel Hayes, the national lead of data-driven productivity for elective care, reports that the new technology has brought powerful insights to NHS operations, particularly in his work with Coventry and Warwickshire.
Process mining analyzes healthcare processes to improve efficiency by examining patient pathways and bottlenecks. One of Hayes’ team’s recent achievements was addressing high rates of missed appointments, or “Did Not Attends” (DNAs). With a shift to sending reminder texts earlier—at 14 and four days before appointments—DNAs dropped from 1,800 to 700 per week. This simple timing adjustment has helped reduce waiting lists and increase patient engagement across the region.
Hayes emphasizes that while cost savings are important, the priority is on making healthcare processes smoother and more supportive for patients, especially when they’re at their most vulnerable. He believes the transformative power of process mining combined with AI-based automation could have a nationwide impact in enhancing both operational efficiency and patient experience across NHS England.
“Dramatic” deficit in skills needed for digital transformation
The UK's manufacturing sector is struggling to find new recruits with the digital skills needed for transformation, according to Stephen Phipson, Chief Executive of Make UK. Speaking at the Advanced Engineering event on 31 October, Phipson highlighted a "dramatic" skills gap as the sector’s biggest obstacle, with 58,000 job vacancies currently unfilled.
An ageing workforce, a decline in apprenticeship numbers, and limited access to European labor have led to a "real squeeze" on essential skills. As companies ramp up automation and digitalization, they’re discovering that many new hires lack the training needed to support these shifts, with many fresh graduates ill-equipped for digitally advanced roles, Phipson said.
The UK government's recently announced Industrial Strategy aims to close this gap, but there are few relevant qualifications in high demand, particularly in emerging fields like circular manufacturing. IMechE President Dr. Clive Hickman echoed these concerns, calling for investment in skill development aligned with industry needs.
While digitization can ease some of these workforce challenges, Phipson highlighted the need for a skilled labor pipeline, suggesting recruitment from nations like India as a partial solution. However, recent immigration policies have made it harder to attract overseas engineers, a restriction he described as politically sensitive but necessary to address for industries like wind turbine production.
On a positive note, Phipson acknowledged that the current government’s stance on manufacturing is promising, with targets to boost the sector from 10 percent to 15 percent of GDP. However, to truly compete on a global scale he said that Britain must improve its approach to scaling innovations domestically, particularly in the race to onshore green technologies.
READ MORE PEX RESEARCH & REPORTS NEWS: