A guide to Process Failure Mode Effects Analysis (PFMEA)
This guide provides recommendations on how to complete a PFMEA
Add bookmarkListen to this content
Audio conversion provided by OpenAI
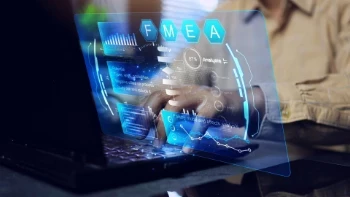
What is a PFMEA?
A Process Failure Mode Effects Analysis (PFMEA) is a structured analytical tool used by an organization, business unit or cross-functional team to identify and evaluate the potential failures of a process.
PFMEA helps to establish the impact of the failure and identify and prioritize the action items with the goal of alleviating risk. It is a living document that should be initiated prior to process of production and maintained through the lifecycle of the product.
PFMEA evaluates each process step and assigns a score on a scale of one to 10 for the following variables:
- Severity — It assesses the impact of the failure mode (the error in the process), with one representing the least safety concern and 10 representing the most dangerous safety concern. In most cases, processes with severity scores exceeding eight may require a fault tree analysis, which estimates the probability of the failure mode by breaking it down into further sub-elements.
- Occurrence — It assesses the chance of a failure happening, with one representing the lowest occurrence and 10 representing the highest occurrence. For example, a score of one may be assigned to a failure that happens once in every five years, while a score of 10 may be assigned to a failure that occurs more frequently, such as once per hour or once per minute.
- Detection — It assesses the chance of a failure being detected, with one representing the highest chance of detection and 10 representing the lowest chance of detection.
- Risk priority number (RPN) = severity X occurrence X detection. By rule of thumb, any RPN value exceeding 80 requires a corrective action. The corrective action ideally leads to a lower RPN number.
Don't miss any news, updates or insider tips from PEX Network by getting them delivered to your inbox. Sign up to our newsletter and join our community of experts.
How to complete a PFMEA?
A simple explanation of how to complete a PFMEA follows below:
- Form a cross-functional team of process owners and operations support personnel with a team leader.
- Have the team leader define the scope, goals and timeline of completing the PFMEA.
- As a group, complete a detailed process map.
- Transfer the process map for the steps of the PFMEA process.
- Assign severity, occurrence and detection scores to each process step as a team.
- Based on the RPN value, identify required corrective actions for each process step.
- Complete a responsible, accountable, consulted, and informed (RACI) chart for the corrective actions.
- Have the team leader on a periodic basis track the corrective action and update the FMEA.
- Have the team leader also track process changes, design changes and other critical discoveries that would qualify and update the PFMEA.
- Ensure that the team leader schedules periodic meetings to review the PFMEA. Based on process performance, a quarterly review may be an option.
Related article: Four easy ways to avoid FMEA mistakes
What are some caveats for PFMEA?
PFMEAs should never be filled out by only one person, it needs to be filled out by the team that owns the process. Buy-in from every team member is required to prevent the PFMEA from becoming an afterthought.
It is a good idea to spend the time to identify which process really needs an FMEA. Conducting too many PFMEAs on non-critical processes will consume resources without returns.
Once the decision is made to pursue a PFMEA, it is critical to include people in the team who have extensive experience with the process and who can share historical data that will prove invaluable while assigning severity, occurrence and detection scores. This step will help to provide a more accurate representation of the immediate to-dos and wish list items the team needs to complete from a risk standpoint to quality and the customer.
It is extremely critical to spend time at the "gemba" or the actual spot where the process takes place, as it is useful to understand in detail each and every process and sub-process that will be part of the FMEA.
As pre-work for the PFMEA, it is wise to have the data for the field failures (failures of the product at a customer location) available with some preliminary analysis completed. Some items, like a Pareto chart highlighting what have been the failure modes for the field failures, can be powerful pieces of information that can add to the validity of the PFMEA.
Related article: 12 essential Lean Six Sigma concepts and tools
A no brainer, but any time there is a change to the process, spec, design or material, the FMEA will need to be updated, and a new RPN value will need to be calculated.
In my opinion, a fixed time interval for reviewing the FMEA of the process must be assigned, with the flexibility to revisit upon a change. This must be a mandatory part of the organization's engineering change management system.
PEX Report 2024 global state of process excellence
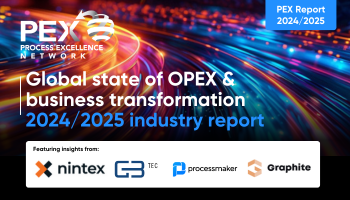
PEX Network's annual report reveals the current state and future trends of process excellence. Based on a study profiling hundreds of global process excellence leaders, the report provides insights on how to leverage innovation, generative AI, and process intelligence to achieve operational excellence, customer-centricity, and organizational growth. Download your copy of the PEX Report 2024/2025 today and benchmark your process excellence journey against your peers.
Download Now