The eight deadly lean wastes: DOWNTIME
Learn what the eight most common types of waste in the workplace are
Add bookmarkListen to this content
Audio conversion provided by OpenAI
Copious amounts of waste can occur in the workplace, particularly in the manufacturing process. Do you know what the eight most common wastes are and how they impact your organization?
Taiichi Ohno, considered the father of the Toyota Production System (TPS), created a lean manufacturing framework based on the idea of preserving or increasing value with less work.
Anything that does not increase value in the eye of the customer must be considered waste, and every effort should be made to eliminate that waste. The following eight lean manufacturing wastes, mostly derived from the TPS, apply universally to businesses today. The acronym for the eight wastes is DOWNTIME, which stands for:
- Defects
- Overproduction
- Waiting
- Not utilizing talent
- Transportation
- Inventory excess
- Motion waste
- Excess processing
Don't miss any news, updates or insider tips from PEX Network by getting them delivered to your inbox. Sign up to our newsletter and join our community of experts.
Defects
Defects are mistakes that require additional time, resources and money to fix. In a manufacturing process, a defect might involve a defective part that has to be remade. Some causes include:
- Poor quality controls
- Poor repair
- Poor documentation
- Lack of standards
- Weak or missing processes
- Misunderstanding customer needs
- Uncontrolled inventory levels
- Poor design and undocumented design changes
Completely eradicating any form of waste is impossible, but defects can certainly be limited by a few measures. These include the application of standardized work plans, more stringent quality control at all levels, a full understanding of work requirements and customer needs, and simple job aids such as checklists.
Overproduction
In some organizations, workers just blindly keep producing, even when those who receive their output either are not ready for it or do not need it. This is a big flaw as it can tie up significant working capital. It is especially common in manufacturing, but it can occur in any workplace situation where there is a bottleneck.
Overproduction may occur due to:- Just-in-case production
- Unclear customer needs
- Producing to a forecast
- Long setup times
- Engineering changes
- Poorly-applied automation
The solution to overproduction is to establish a reasonable workflow for the benefit of the customer. Ensure there are well-established procedures in place for every process in your organization, and if necessary, implement new processes to keep work from backing up behind particular bottlenecks in the organization.
Read more: Why lean six sigma is poised for a comeback in 2023
Waiting
Waiting occurs whenever work has to stop for reasons that can include the next person in line being overwhelmed, something breaking down, waiting for approval or materials, or running out of something. Other causes can include:
- Unbalanced workloads
- Unplanned downtime
- Long setup times
- Producing to a forecast
- Insufficient staffing
- Work absences
- Poor process quality
- Poor communication
Whatever the cause, some workers have to wait for a bottleneck to be cleared. One way to address this is by ensuring there is adequate staffing to handle the workload at the bottlenecks, which some managers may target as a source of monetary waste.
Not utilizing talent
While it is not part of TPS' seven wastes, failing to utilize talent is on the rise in businesses today. Not using or under-using people's talents, skills and knowledge can have a detrimental effect on an organization.
Companies can reap great benefits when they recognize the value of skills and improvement ideas from all levels of the business, and can suffer when they are not effectively engaging in the process. This can typically be seen with:
- Assigning staff to wrong tasks
- Wasteful admin tasks
- Poor communication
- Lack of teamwork
- Poor management
- Insufficient training
If the above list sounds oddly familiar, it is normal. Many of these failings are the same ones that result in a lack of employee engagement, which can hamstring any organization's productivity. Key solutions include empowering your employees, stopping micromanagement and increasing training.
Read more: An introduction to Gemba Kaizen
Transportation
Transportation is waste caused by moving things around. This is less of a problem in a business office than in a manufacturing plant, since most of what white collar workers "transport" can be sent by email for example.
Otherwise, too much transportation tends to increase costs, waste time, raise the likelihood of product damage and deterioration and can result in poor communication. In general, transportation waste can be caused by:
- Poor plant or office layout
- Unnecessary or excessive steps in the process
- Misaligned process flow
- Poorly-designed systems
Limiting transportation waste can be easily addressed by common-sense efforts such as simplifying processes, repairing physical layouts, handling products less often and making distances between steps as short as possible.
Inventory excess
Inventory excess occurs when there is supply in excess of real customer demand, masking real production. Causes include:
- Overproduction and buffers
- Poor monitoring systems
- Mismatched production speeds
- Unreliable suppliers
- Long setup times
- Misunderstood customer needs
Read more: Four steps for implementing continuous improvement
Motion waste
Motion waste is defined by any excess movement caused by employees or machines that does not add value to the product, service or process. Typical causes include:
- Poor process design and controls
- Poor workstationor shop layout
- Shared tools and machines
- Workstation congestion
- Isolated and siloed operations
- Lack of standards
The solution here is to rearrange layouts to decrease the distance between stations and make it easier to reach things that are often used.
Excess processing
Excess processing often occurs when multiple versions of the same task are created, when an organization processes more than is required or as a result of long-winded poorly designed processes. Examples include:
- Excessive reports
- Multiple signatures
- Reentering data and duplicated data
- Lack of standards
- Poor communication
- Overdesigned equipment
- Misunderstanding of the customer's needs
- Human error
All of these unnecessarily increase your costs, time and resources. You must first examine and map your organization to analyze the processes in order to fix them. Standardize processes, empower employees and eliminate unnecessary documentation, sign-off processes and meetings.
Systematic elimination of these wastes can result in faster processes, lower costs, higher quality, happier workers and, most importantly, happier customers.
The 26th Annual OPEX Week: Business Transformation World Summit | post show report
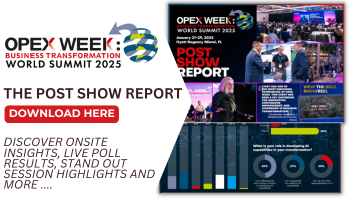
Over 550 transformation leaders from 200 companies across 17 countries gathered to share innovations and stories at OPEX Week 2025. The three unforgettable days sparked groundbreaking ideas and invaluable connections. Don't worry—we've got you covered with a full recap of the 2025 OPEX Week. Download the post-show report here.
To view this content, please fill out the form to register and become a member.
Or, if you're already a member, sign in below to view.
Please note: That all fields marked with an asterisk (*) are required.