Lean Six Sigma enhances combat readiness in US military
Lean Six Sigma is driving tangible improvements in efficiency and operational readiness in the US Army
Add bookmarkListen to this content
Audio conversion provided by OpenAI
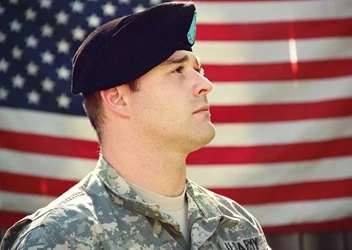
Lean Six Sigma is enhancing combat readiness in the United States military. In the latest iteration of an ongoing partnership between the United States Military Academy West Point and Tobyhanna Army Depot (TYAD) – part of the US Army Communications-Electronics Command – three senior groups of cadets finished Lean Six Sigma Green Belt projects.
The initiative, now in its 14th year, aims to educate cadets about tangible improvements in efficiency and operational readiness while providing them with invaluable exposure to real-world logistics challenges. The three groups operated with members of Team Tobyhanna as they followed the five-step Lean Six Sigma method of Define, Measure, Analyze, Improve and Control (DMAIC).
This year’s presentations were focused on Hazardous Materials (HAZMAT) Reduction, Production Order Traveler Accuracy and System Throughput within TYAD’s C4ISR Finishing Division.
Don't miss any news, updates or insider tips from PEX Network by getting them delivered to your inbox. Sign up to our newsletter and join our community of experts.
Tangible improvements in efficiency and operational readiness
The partnership between West Point and TYAD represents a strong synergy of academic excellence and real-world military logistics expertise, said Christopher Musso, TYAD’s director of quality management.
“By implementing Lean Six Sigma methodologies with measurable objectives, the Capstone projects have delivered tangible improvements in efficiency and operational readiness, while providing the cadets with invaluable exposure to real-world logistics challenges,” Musso added. “The cadets have not only developed solutions that enhance our current operations, but they have also experienced firsthand the complexity of military industrial processes.”
The collaboration exemplifies commitment to developing both tomorrow’s leaders and today’s operational excellence (OPEX) within the Army and the organic industrial base, Musso said.
The goals of each team varied:
- The HAZMAT Reduction team set out to improve the Hazmat Disposal Process from 11.24 percent waste to 5.62 percent.
- The Production Order Traveler Accuracy team aimed to improve the accuracy and reduce delays of the TYAD traveler documents.
- The System Throughout team wanted to reduce the planned versus actual repair cycle time (RCT) from an average of 59 to 20 days to improve process efficiency and increase the sigma quality level from 0.81 to 1.25 for production orders.
Benefits of Lean Six Sigma in US military
Cadet Calahan Barker, a member of the HAZMAT Reduction team, said having the opportunity to apply what they’ve learned in the classroom to real-life situations adds to the educational experience. “These projects are a good experience because it allows cadets to put everything we’ve learned in class to use. To see all of the things you've learned in class come to life makes it more real.”
Depot Commander Col. James L. Crocker championed the longstanding relationship between Tobyhanna Army Depot and West Point as well as the benefits of Lean Six Sigma within the US military.
“By welcoming cadets on post, the next generation of Army logisticians come face-to-face with what they’ve learned in the classroom and depot artisans come face-to-face with the next generation of warfighters whom their work is supporting,” he said. “Your work will help to drive meaningful conversations across the depot about how we can continue to work towards becoming the most efficient organization possible.”
PEX Report 2024 global state of process excellence
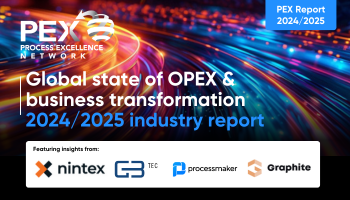
PEX Network's annual report reveals the current state and future trends of process excellence. Based on a study profiling hundreds of global process excellence leaders, the report provides insights on how to leverage innovation, generative AI, and process intelligence to achieve operational excellence, customer-centricity, and organizational growth. Download your copy of the PEX Report 2024/2025 today and benchmark your process excellence journey against your peers.
Download Now