The intelligent operations model
Intelligent operations leverage digital acceleration to transform traditional workflows into efficient, adaptive and data-driven processes
Add bookmark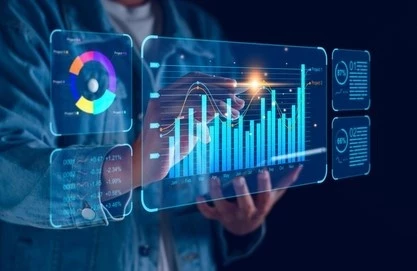
In today’s rapidly evolving business landscape, the purpose of intelligent operations is to leverage digital acceleration to transform traditional workflows into highly efficient, adaptive and data-driven processes. By integrating cutting-edge technologies such as robotic process automation (RPA), advanced analytics or artificial intelligence (AI), organizations can achieve unparalleled levels of operational excellence.
This transformation not only enhances efficiency and productivity but also fosters innovation and agility, enabling businesses to respond swiftly to market changes and customer needs. Intelligent operations powered by digital acceleration are crucial for companies aiming to stay competitive and drive sustainable growth in an increasingly digital world.
Don't miss any news, updates or insider tips from PEX Network by getting them delivered to your inbox. Sign up to our newsletter and join our community of experts.
Traditional versus intelligent operations
The primary difference between traditional and intelligent operations models lies in the integration and utilization of advanced digital technologies. Traditional operations typically rely on manual processes and basic automation, where workflows are mapped and executed with limited real-time data insights. This often leads to inefficiencies and reactive problem-solving.
There are new business enablement and transformation challenges that demand continuously collecting and analyzing data to optimize processes in real-time, enabling proactive decision-making and significant enhancements in efficiency, accuracy and speed. Intelligent operations foster a collaborative environment where human skills are augmented by technology, leading to more innovative solutions and higher overall productivity.
READ: PEX Guide: What is operational excellence?
Digital accelerators in intelligent operations
An ecosystem that combines various digital accelerators, such as RPA, process mining, chatbots and advanced analytics enhances a model of intelligent operations. These technologies work together to automate routine tasks, uncover inefficiencies and provide insights for continuous improvement, thereby driving business transformation. For this purpose, a digital operations accelerator is considered any type of technology that adds capability without being part of the operational systems. The differences and evolutions of operational models can be observed according to a set of impacted dimensions.
READ: Process mining and the growing role of generative AI
Relevance
In traditional operational models, the incorporation of feedback from stakeholders (e.g. clients, partners) is limited, effortful and slow. Conversely, the use of digital acceleration technology in intelligent operational models not only facilitates the incorporation of feedback at scale and speed but can also transform work methods. The relevance provided by intelligent operations is perceived through improved processes and execution, where stakeholders feel involved because they influenced the process design, attributing relevance to it. By integrating digital accelerators, companies can achieve significant improvements, such as reducing operational costs, decreasing process cycle times and enhance overall productivity. These measurable benefits underscore the importance of adopting intelligent operations.
Outcome
In a traditional operational model based on process mapping, the outcome of process execution is always impacted by the bias between how the process was mapped and how it is actually executed, as well as its variance. In contrast, in an intelligent operational model, digital accelerators enable the transparent and objective description of how processes are executed. With a clearer understanding of reality, the outcome is different and free from the distortion found in traditional operations.
Efficiency
Identifying errors in process execution in traditional operational models is inherently reactive. Error identification triggers a reaction because continuous improvement work is based on potentially distorted mapped processes. In the context of intelligent operations, not only is it possible to transparently visualize how processes are executed in the real world, but also to simulate future scenarios by altering certain factors that influence process execution (e.g. number of dedicated resources) to achieve behavioral changes and business impacts.
Experience
The experience of various parties involved in process execution is also different in an ecosystem of intelligent operations supported by digital accelerators. Unlike traditional operations, where the level of operational customization is high and interaction with record systems is complex, intelligent operations provide additional capabilities that make user experiences simpler, faster and even change the way of work. A call center agent working directly with a CRM system often must manually input data, search for information and perform repetitive tasks, which can be time-consuming and prone to errors. In contrast, using a chatbot assistant combined with RPA streamlines these tasks by automating data entry, quickly retrieving information and standardizing responses. This integration simplifies the agent’s workflow, significantly increases the speed of handling customer inquiries and ensures a consistent quality of customer care, ultimately leading to improved efficiency and customer satisfaction.
Intelligent operations roadmap
There is a roadmap for implementing intelligent operations that can be broken down into the following steps:
1. X-ray as-is
Action: Use tools like process mining to map existing workflows and identify areas for improvement.
Outcome: Gain a clear understanding of current process performance and identify bottlenecks or inefficiencies.
2. Identify digital accelerators
Action: Determine which technologies (e.g., RPA, chatbots, advanced Analytics) can address specific inefficiencies.
Outcome: Select the most appropriate digital accelerators tailored to your organization’s needs.
3. Pilot projects
Action: Start with small-scale pilot projects to test the effectiveness of digital accelerators in a controlled environment.
Outcome: Validate the potential benefits and make necessary adjustments before scaling up.
4. Develop a skilled workforce
Action: Invest in training and development programs to upskill employees in using new technologies and understanding data-driven decision-making.
Outcome: Ensure your workforce is equipped with the necessary skills to operate and leverage digital tools effectively.
5. Change management and stakeholder engagement
Action: Implement a change management strategy that includes clear communication, stakeholder involvement and addressing resistance.
Outcome: Facilitate a smoother transition by ensuring all stakeholders understand the benefits and are on board with the changes.
6. Scale and optimize
Action: Gradually scale successful pilots across the organization, continuously optimizing processes based on data-driven insights.
Outcome: Achieve widespread improvements and maintain agility by regularly refining processes.
7. Monitor and measure
Action: Regularly monitor performance metrics to ensure ongoing improvements and adapt to changing market conditions. Value realization measurement is a powerful weapon to proceed and keep growing.
Outcome: Sustain long-term success by keeping operations aligned with strategic goals and responding proactively to new challenges.
Intelligent operations will be essential for operational excellence
In an ecosystem of intelligent operations, all functions are impacted by digital acceleration with the aim of enhancing human capacity, requiring new skills and changes in mindset. It becomes normal to combine manual work by humans with automated tasks produced by robots, as well as virtual assistants that support front-office operations in client interactions, improving the experiences of both clients and employees. Moreover, from an analytical perspective, transparent observation of how processes are executed in the real world leads to recommendations that drive business transformation with high impact.
Executive and operational functions are exposed to facts derived from suggestive technology, counteracting biases often produced by perceptions which represents one organizational challenge.
READ: 5 operational excellence trends for 2024
Looking ahead, the integration of AI-driven decision-making, process mining for enhanced transparency and real-time data collection will further revolutionize intelligent operations. These innovations will enable even greater efficiency, accuracy and responsiveness, driving the next wave of operational excellence.
As businesses continue to navigate an increasingly complex and digital landscape, embracing intelligent operations will be essential for achieving operational excellence, driving innovation and maintaining a competitive edge.
All Access: AI in PEX is 2025
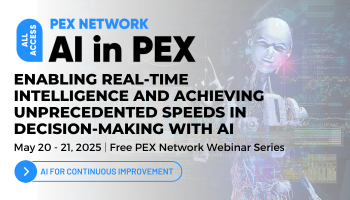
All Access: AI in PEX 2025 is designed to address these challenges and empower organizations to successfully integrate AI into their process improvement initiatives. The content series will bring together industry experts, thought leaders, and practitioners to share insights, best practices, and real-world case studies.
Register Now