PFMEA: Laying the groundwork for robust processes
PFMEA is an essential tool for enhancing process reliability and quality
Add bookmark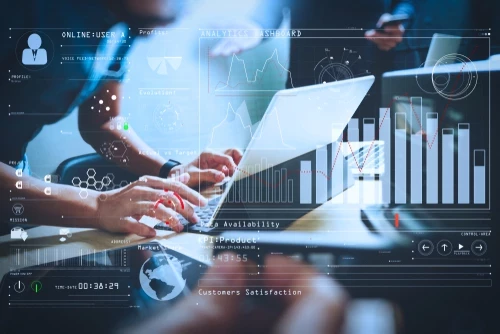
In my career as a process excellence professional, I vividly remember my early years delving into process improvement. I was captivated by the tools and techniques used to identify root causes and areas of waste. Witnessing a Kaizen team swiftly assess a product or process for substantial improvement was particularly fascinating, especially since I was relatively new to these tools and methodologies.
I recall instances where quality professionals and technicians struggled to determine the reasons behind defects, resulting in hours or days of rework and an even longer backlog. Technicians worked tirelessly to meet demand, while upper management prioritized the product over the process. However, behind all of the chaos lies the “silent machine” – otherwise known as “the process,” which is rarely fully understood at a systems level.
Don't miss any news, updates or insider tips from PEX Network by getting them delivered to your inbox. Sign up to our newsletter and join our community of experts.
To gain a better understanding of the various processes in an organization, there are a handful of tools and methodologies that can facilitate improved comprehension of the interdependencies, areas of risk and potential outcomes. Process failure modes and effects analysis (PFMEA) is an “early warning” system. Most of us in the continious improvement community are familiar with FMEA and its capabilities. On the other hand, PFMEA also plays an equally vital role in quality management and risk assessment. Its focus on the process helps to identify potential failures, inefficiencies and associated risks, which is crucial in evaluating the cost of poor quality (COPQ). By exploring the background of PFMEA, providing practical applications with example scenarios and highlighting its synergy with COPQ, leaders and process excellence professionals can gain a fresh perspective on PFMEA.
The objective of PFMEA is to anticipate potential issues before they occur, allowing organizations to implement corrective actions proactively, thus reducing defects and driving down COPQ. This preventive approach helps in enhancing the reliability and quality of processes, reducing downtime and minimizing costs associated with defects and failures.
It originated from the broader FMEA methodology, which was initially developed by the aerospace industry in the 1940s and later adopted by the automotive sector and other industries. As in FMEA, PFMEA is a systematic method for identifying and prioritizing potential failure modes within a manufacturing or business process.
PFMEA in action
While assigned to an overseas aircraft component repair facility, the lead time for overhauling a specific type/model/series of aircraft engine was more than two months before the implementation of PFMEA, process maps and resulting Kaizens. Given that each aircraft is equipped with four unique engines, the lengthy overhaul process posed a dangerous risk to the aircraft’s mission and led to soaring costs. The organization is one of three overhaul facilities worldwide and manages the comprehensive overhaul of aircraft engines, from induction and inspection to disassembly into modules, unique work cell overhauls, reassembly, testing, inspection and preservation for global shipment. This meticulous process involves thousands of detailed, documented steps to ensure flight safety.
Ideally, a PFMEA should be accomplished at the beginning stages of a process design, long before the facility or factory goes live. The best-case scenario is to assemble a team from all aspects of the area of focus, design the process in the ideal state and then build the PFMEA from there. In reality, however, a PFMEA is built out of necessity as problems become increasingly complex and impact profit, customer base and safety. Technical problems from a manufacturing perspective include delays, interruptions, shortages, specifications out of tolerance and many more. The method of building a PFMEA involves a cross-functional team of professionals such as engineers, operators, shipping and receiving clerks, maintenance, expeditors, quality and any other role that directly or indirectly influences the process. There is no specific role designated to lead the PFMEA team, except that the lead person has the authority to provide resources and capability, remove barriers and ensure the PFMEA progresses through to completion.
Referring to the aircraft engine case study, the PFMEA team began with gap analysis and introductions, built a charter, agreed on a schedule and established ground rules to keep the project moving forward. The team analyzed each step of the given sub-process. Then, it was reviewed to identify failure modes, assess the severity and likelihood of each failure and determine the detectability of failures. These factors were then combined into a risk priority number (RPN) to prioritize actions.
When identifying potential failures in the process, particular attention was focused on the inter-relationships between work cells and JIT. It was soon apparent that the linear flow of the overall process was designed to fail from the start. For a module to move down the line, it had to wait for resources consumed by parts before and after. From a 1000-foot view, it all looked quite efficient, yet when performing Gemba walks, it was painful to see one work cell operating at maximum output while another was idle. The need to balance the line could not have been overstated.
The 8 steps of PFMEA
Putting PFMEA into action, the overall process needed to be broken into sub-processes by following the below steps.
1. Examining the process
A team was assigned to each sub-process and performed process maps, spaghetti diagrams, handoffs, queue times, consumables, hazardous materials, tools and every input for the process. Delving even deeper, personnel training and qualifications were reviewed with gap-analysis, personnel turnover and onboarding, just to name a few. It was crucial to understand and document the process flow and to make it visual.
2. Identifying modes of failure
In our process, we carefully identified all potential failure points. Based on past experiences, we found that background processes are often overlooked and can be extremely costly. Consider calibration and hazardous materials. Precision measuring equipment (PME) must be regularly calibrated, which means the need to plan for replacements. If a tool is sent for calibration without a replacement, it can cause interruptions in the process. The same applies to hazardous materials. Dealing with expired sealants, outages and hard-to-find compatibility information can take up valuable time. These are the “failure modes” that we needed to consider, including errors related to material quality, machine malfunctions, human errors, environmental factors and more.
3. Reviewing causes of failure
To further elaborate, let’s take the example of hazardous materials and delve into the underlying cause of a tube of expired sealant. This involved investigating the organization’s hazardous materials shelf-life tracking program. Additionally, researching the safety data sheets and the EHS program were necessary to gather compatibility information. Once each failure mode was identified, it was important to determine the root causes, which are the factors that could potentially lead to the failure mode. It is crucial to understand these causes to develop effective preventive measures.
4. Assessing the effects of each failure
Once the team has identified the failure and its root cause, they need to assess the extent of the impact of each defect. Let’s consider the case of expired sealant. If the technician used the sealant without realizing it was expired, it could fail and result in various catastrophic events. On the other hand, if the technician recognized the expired sealant and reported it to the hazardous material custodian, a replacement tube could be obtained immediately, if available in stock. However, if it were not in stock, this failure would lead to process delays. It’s important to consider the consequences of each failure mode, understanding how it affects the process, the product and the end-user. The severity of each failure mode’s effect is typically rated on a scale from 1 to 10, with higher values indicating more severe consequences.
5. Calculating RPNs
To calculate the RPN, the team determines the severity of each failure. Historical data is a key component in this determination. Team members can research reports from manufacturers and various agencies to help determine the severity. This can also be used to determine the frequency of occurrence if no other data is available. Ease and methods of detection are the final elements. Thus RPN= SOD (severity, occurrence and detectability)>
6. Building an action plan
After determining the RPN, it is crucial to take concrete steps. For example, when dealing with an expired tube of sealant, one action could be the implementation of administrative controls, such as creating written procedures, adding the item to a checklist, or including it in the audit database managed by the quality department. The next step is to develop an action plan based on the RPN, prioritizing the most critical risks for immediate attention. This plan may involve process redesign, the addition of quality checks, personnel training, or changes to materials or equipment. It's important to assign responsibilities and set deadlines for implementing these actions.
7. Following up
Team leads, supervisors, the continuous improvement team and the quality team play a key role in this step. Collectively, they monitor the effectiveness of the changes to the process. For example, if a checklist was implemented, the team lead or supervisor should be performing Gemba walks periodically to ensure that the new process is being adhered to and that it is understood. Additional tweaks may be necessary. The key here is to monitor the effectiveness of the changes from the previous step. These action(s) should have minimized or eliminated the risk.
8. Performing updates
Depending on the organization, the continuous improvement team is responsible for updating various documents as changes occur. It’s important to keep the PFMEA updated to reflect the ongoing improvements and accurately depict the current state of the process, ensuring that the analysis remains a dynamic and accurate record of the process.
PFMEA is an essential tool for organizations aiming to enhance the reliability and quality of their processes. By proactively identifying potential failures and implementing corrective actions, companies can significantly reduce the costs associated with poor quality, improve customer satisfaction and ensure efficient and reliable processes. Understanding the relationship between PFMEA and COPQ, along with its differences from FMEA, provides a comprehensive approach to quality management and risk assessment.
All Access: AI in PEX is 2025
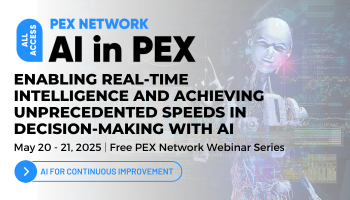
All Access: AI in PEX 2025 is designed to address these challenges and empower organizations to successfully integrate AI into their process improvement initiatives. The content series will bring together industry experts, thought leaders, and practitioners to share insights, best practices, and real-world case studies.
Register Now