The art of process improvement: An analogy for efficiency & automation
Explore the critical process flows that help find efficiencies and transform operations
Add bookmarkListen to this content
Audio conversion provided by OpenAI
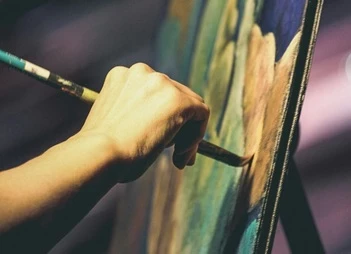
If you’ve ever had the privilege of watching an artist working on an oil painting or even enjoyed a Bob Ross video or two, you will have seen one of the vital techniques that elevates their work above the average.
They’ll be adding fine touches to a single element, focused on one part of the picture, but then they’ll step back. They may return to that tiny detail, but for a moment they’ll consider the section they’re working on as part of the whole canvas. That’s the key to getting those kinds of details right – knowing how they work within the big picture.
This is a great approach to keep in mind when we’re considering process improvement and automation.
Oftentimes, the technical and process teams tasked with these ventures are laser-focused on a particular area of the business. A department or business function will be identified for improvement, usually in an effort to reduce costs and increase outcomes, and the experts will hone in on the processes and practices that could be refined to achieve those goals.
In all fairness, they will undoubtedly identify some savings that can be made, but usually it’s limited to that one division. The process improvement team’s efforts will be siloed and for all their expertise, the results won’t have much applicability beyond the boundaries that they were set in the beginning.
Tackling process silos
In our painter analogy, we may have one really happy tree, but the rest of the forest will be lacking attention. These siloed solutions can easily miss the context of the operations – the wider canvas – and so overlook the real efficiencies that could be implemented.
For every business group, team or department, some inputs and outputs should be considered. Their processes rely on systems, resources and data from other departments or even external companies. For every process they execute, there are other processes feeding into them and flowing on out of them. It’s this greater end-to-end flow of processes that really needs to be considered before any process improvement tools can be effectively deployed.
The practice of identifying these key phases of operations is called process ‘chunking’ and helps identify the overall flow of the business.
Seeing the bigger picture
When an artist steps back to consider the whole canvas, they’re looking at things like composition and balance. How do the elements work together, and what needs attention next? The same applies when we consider process improvement and automation.
Have the process improvement teams take a step back and identify the key business phases and consider the essential flows of information, resources and effort. Where are the breakdowns most apparent? Where are delays showing up, and what areas of waste can easily be identified? By exploring the overall efficiencies before trying to dive into the micro-detail of operational processes, your process people can get a better idea of where to focus their efforts, or at least where to start.
Understanding these critical process flows will also help find efficiencies that might not be so apparent at an operational level. Process inputs can have a significant impact on the way a process functions, so exploring how they are generated and delivered can result in effective improvement strategies that might not be found if the focus was exclusively on one department or workgroup. Solving data routing bottlenecks in one area can result in faster process execution in other parts of the business by freeing the flow-on teams to work with greater velocity.
Developing better process solutions is an art form. Just like a great painter, the teams responsible should be able to step back and consider the bigger picture and focus their efforts on the elements that will make your operations shine.
There are always plenty of processes that you can work on to increase efficiency and improve outcomes, but don’t forget to consider the big picture before investing too much energy in the details.