Manufacturing firms reduce downtime & operational costs with digital twins
Manufacturing firms are leading the way in digital twin adoption
Add bookmarkListen to this content
Audio conversion provided by OpenAI
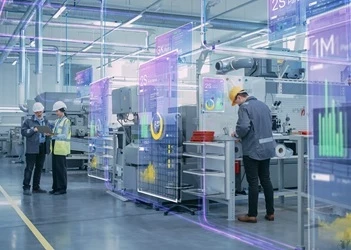
Over 40 percent of manufacturing firms are piloting digital twin technology with full rollouts continuing to emerge, according to the Manufacturing IT/OT Trend Report 2025.
The report compiles the findings of a survey of decision-makers and senior managers ahead of the Manufacturing IT/OT Summit Europe in September. It details the most common benefits of adopting digital twins, with almost two-thirds of respondents citing reduced downtime and operational costs.
This is in the wake of separate research from IDS-INDATA which showed how the staggering financial and operational impact of unplanned manufacturing downtime emphasizes the critical need for digital transformation.
Don't miss any news, updates or insider tips from PEX Network by getting them delivered to your inbox. Sign up to our newsletter and join our community of experts.
Digital twin investment is growing in manufacturing
The Manufacturing IT/OT Trend Report 2025 indicates cautious but growing investment digital twins in manufacturing. Just shy of 41 percent of organizations are in the pilot phase of digital twin implementation. Meanwhile, 20 percent report full integration and 15 percent use it in selected areas. Another 15 percent are planning implementation, with only 10 percent currently having no plans to do so.
Of the organizations that have used digital twin technology, 65 percent have seen downtime and operational costs reduced. More than half (55 percent) report improved predictive maintenance, while 40 percent have achieved better collaboration. Enhanced planning and efficiency (35 percent) and real-time simulation (25 percent) follow. Just 15 percent saw no measurable impact so far.
Manufacturing leads the way in digital twin adoption
Almost a third (30 percent) of organizations are spending over $10 million on digital twin technology, with manufacturing leading adoption. That’s according to recent research from Siemens and S&P Global.
The pair carried out a study of 907 businesses across seven countries, revealing a sharp increase in “industrial virtual metaverse” technology investments. These technologies provide a network of virtual replicas that mirror physical factories, supply chains and product development processes, using digital twins – detailed virtual models of physical objects and processes – in combination with real-time sensor data and artificial intelligence (AI) to optimize manufacturing processes, predict maintenance needs and simulate new product designs.
“The fundamental technologies that enable the industrial metaverse are being rapidly developed worldwide,” commented Peter Koerte, CTO and chief strategy officer at Siemens AG. “Many companies are not only experimenting with these technologies but are already employing and scaling concrete use cases that demonstrate the added value of the industrial metaverse.”
Task mining – unlocking new possibilities in process optimization: Industry report 2025
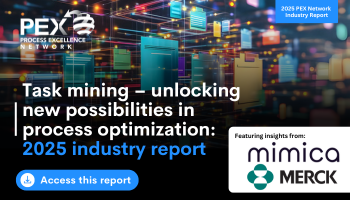
Task mining is experiencing robust growth, driven by the increasing need for process optimization and automation across diverse sectors. The market, estimated at US$2 billion in 2025, is projected to exhibit a compound annual growth rate (CAGR) of 25 percent over the next eight years, reaching an impressive $10 billion by 2033, according to Market Report Analytics.
Download this report to explore the task mining landscape and learn how it unlocks new opportunities in process optimization!
Download Now