Achieving OPEX through advanced construction technology
Emerging construction technologies are reshaping OPEX within the construction industry
Add bookmarkListen to this content
Audio conversion provided by OpenAI
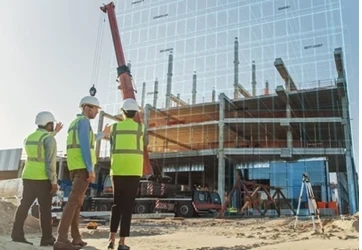
Operational excellence (OPEX) is the ultimate benchmark for industries striving to improve performance, lower expenses and achieve better results. Emerging technologies have rewritten the rules of the construction sector, which has traditionally relied on hands-on work and complicated coordination.
Automation, robotics, digital modeling and real-time data integration signify a ‘new era’ in construction technologies, offering a formerly unimaginable level of precision and productivity. These innovations change the face of construction and provide a roadmap to excellence that different industries can follow to transform their operations.
Don't miss any news, updates or insider tips from PEX Network by getting them delivered to your inbox. Sign up to our newsletter and join our community of experts.
Enhancing construction efficiency and accuracy via technology
The construction industry has adopted advanced technologies like computer-aided design (CAD) to overcome perennial inefficiencies characterized by high costs and project delays. Whereas traditional technology increased design precision and streamlined the drafting process, the new innovations that have been integrated into the industry of building information modeling (BIM) and robotics in construction, among others, further changed how the construction industry works by enhancing collaboration, accuracy and overall productivity.
Autonomous construction vehicles
Autonomous construction vehicles, self-driving bulldozers and excavators transform the site. These vehicles use GPS, sensors and the most recently evolving tool, artificial intelligence (AI), to navigate and execute their tasks accurately.
A McKinsey report states that automation can improve construction performance by up to 50 percent. This way, stakeholders can save huge costs and complete projects much faster. Workers would also not be exposed to poor working conditions on the sites, improving workplace safety.
Robotics in construction
Robotics in construction increases speed and covers key labor gaps. Laying six-times as many bricks as humans, these robots, including semi-automated masons (SAM) and bricklayers, dispense concrete and conduct site inspections.
For example, Grand View Research estimates that the global construction robotics market was worth US$1,028.6 million in 2022. In fact, researchers believe that there will be further growth at a compound annual rate of 17.5 percent by 2030. This indicates the rising need for technologies that enhance the productivity and quality of construction projects.
Laser scanning and surveying tools
Laser scanning technologies can produce precise 3D models of construction sites to help with better planning and tracking of the project. For instance, LiDAR technology absorbs most errors to help improve site assessments. It also makes resource allocation easier and practical, hence reducing material wastage. These technologies are very popular nowadays in all sectors because they are accurate.
Watch Lisa Williams, global operations talent strategy and employee experience director, manufacturing and engineering operations at Dow, discuss embracing new technology
How CAD solutions improve construction workflows
CAD solutions have greatly influenced construction workflows. This technology enables detailed design and simulation, enhances communication and minimizes the chances of mistakes. So, let’s explore how these CAD solutions optimize construction workflows.
From CAD to BIM
BIM is the evolution of 2D CAD techniques. The CAD produces 2D drawings, while the BIM produces 3D models and information on materials, time and cost. This mix of tech enhances stakeholder collaboration, improves project efficiency and reduces errors.
Integration with AR and VR
The use of CAD combined with augmented reality (AR) and virtual reality (VR) improves visualization. AR and VR apps enable stakeholders to experience projects virtually long before they are constructed physically. This is useful in the detection of any potential problems. As per PwC, VR and AR in construction and real estate could generate $1.5 trillion for the global economy by 2030. This shows that these technologies have the potential to reduce costs, increase efficiency and improve decision-making in the construction and real estate industries.
Accelerating project timelines through streamlined workflows
Construction technologies are practical tools that increase the completion time of construction projects. By organizing work effectively and eliminating repetitive tasks, these tools help deliver projects faster than traditional ones. Here is how this works:
Modular and prefabrication techniques
Modular construction, which entails building components being constructed away from the construction site, has been widely embraced for its time efficiency. The Modular Building Institute revealed that modular projects are completed 30 percent to 50 percent faster than traditional construction. This approach also minimizes waste and is more sustainable. For instance, Marriott International constructed a 168-room hotel in New York using the modular construction method and completed it within 90 days, a record time.
3D printing in construction
3D printing has become one of the most effective ways of creating complex structures that can be constructed quickly and at minimum costs. The first 3D-printed residential community in Mexico showed that houses could be built within 24 hours, thus reducing the cost of labor and time.
This technology also allows for the development of unique designs that would be impossible to achieve through conventional construction techniques, advancing the boundaries of architectural art. 3D printing reduces material consumption, making the construction industry more sustainable and helping solve ecological deficit problems.
Watch Pradheep Kileti, director at National Grid, reflect on balancing operations and innovation
Using digital twin technology for informed decision-making in construction
Digital twin technologies represent a new change in how construction projects will be monitored and managed. Creating a digital twin of physical assets can leverage immediate insights to improve decisions and operational efficiency. Here’s how that happens:
- Real-time monitoring and predictive analytics: Digital twins allow for real-time monitoring of construction projects. Performance data is collected from sensors within physical structures and then analyzed for predictive maintenance and fault detection.
- Lifecycle management: Digital twins support the entire life cycle of a project: design, construction, maintenance and demolition. Such a holistic perspective enables the better utilization of resources to achieve maximum longevity of assets, which aids cost economy and sustainability. A Deloitte report adds weight to this assertion when it states that companies could reduce operational costs by up to 25 percent since it significantly reduces forecast errors.
Advanced construction technologies have started remolding the face of OPEX within the construction industry. From autonomous vehicles and robotics to CAD solutions and digital twins, technologies increase efficiency and precision and improve decision-making. These can be implemented to transform operations inside an organization and bring success if effective communication is fostered.
The concepts derived from technological development in the building industry are significant and extend far beyond this sector itself to become relevant to manufacturing, healthcare, finance and technological professions. In an environment of growing competition, there is no alternative but to adopt them.
All Access: BPM Business Process Management 2025
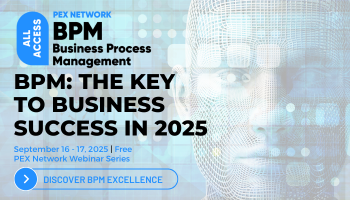
Business process management (BPM) is a discipline that helps organizations improve their efficiency and effectiveness by streamlining their processes. In 2025, BPM will be more important than ever as organizations look to reduce costs and improve customer satisfaction.
All Access: BPM 2025 from PEX Network will help professionals get an understanding of the latest developments in BPM, including how to identify and improve key processes, how to implement BPM technology, and how to measure the success of BPM initiatives.
Register Now