Why continuous improvement is a facilitator to organizational transformation
Involving customers and employees in the transformation strategy is key to success and driving innovation, says Vikram Mehta, Head of Continuous Improvement at Maersk
Add bookmark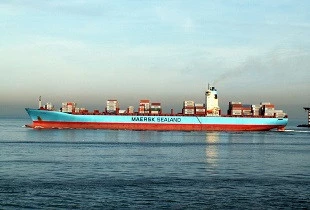
PEX Network caught up with Vikram Mehta, head of continuous improvement at global shipping giant Maersk, ahead of his presentation at upcoming online summit BPM Live. Mehta discusses the importance for businesses to implement continuous improvement, his recommendations for organizations to succeed in their process excellence initiatives and how Covid-19 impacted continuous improvement efforts at Maersk.
Mehta has been part of the A.P. Møller – Mærsk A/S (Maersk) group for more than eight years and heads up the continuous improvement team that leads transformation, supply chain logistics processes, training, e-commerce activities and finance operations in north-west Europe.
Mehta will discuss creating a culture of continuous improvement in the front end at the annual BPM Live event, which takes place online on 29 September – 02 October 2020. Register for free here and join his live presentation.
PEX Network: Why should companies implement continuous improvement?
Vikram Mehta: Continuous improvement is a must for organizations as it facilitates innovation and helps organizations transform and become more efficient. Ultimately, it leads to improvements in customer satisfaction and employee engagement, as well as helping organizations grow organically which is important in today’s economic climate.
Continuous improvement helps organizations benefit from a first mover advantage and allows them to adapt to new elements in the market such as the latest global technology or a crisis. It allows organizations to move fast and make changes quickly. A well-structured continuous improvement team can have significant positive impact on employee and customer satisfaction.
PEX Network: What would be your recommendations for organizations to succeed in their continuous improvement program?
VM: It is important for organizations to start by acknowledging there is always room for improvement and go bottom up. They should ask their customers what they need and what would work for them, because these are the areas where efforts should be invested.
They should also involve their employees in their strategy for continuous improvement. Organizations should consider viewpoints of customer-facing staff who form a major part of their workforce and are closest to the customers.
They should see continuous improvement as an investment instead of a cost. Like any other investment, they should put good efforts in the beginning and expect good returns, but also spend time on getting the strategy and basics right. They should not reinvent the wheel where things are working well already and prioritize initiatives with maximum results and minimum effort or change.
The world of continuous improvement is changing. Many methodologies used 10 and 20 years ago are still being used, but a lot of newer approaches such as agile, AI and minimum viable product have emerged, and are becoming increasingly important in today's rapidly changing business environment.
PEX Network: How has Covid-19 impacted the execution of the continuous improvement program at Maersk?
VM: We had to quickly adapt to changing business, customer and employee needs in order to stay ahead in the market. We were able to immediately bring in new ways of communications, engagement and reaching out to customers.
We have a robust business continuity planning setup and change management team supported by flexible IT solutions. We also have a well-balanced continuous improvement team made of a good mix of strong experienced people and new people with new ideas, technologies and knowledge. We were prepared with a contingency for a situation of this nature and have continued with the mind-set of business as usual from day one.
At Maersk, we have a strong pipeline of continuous improvement projects and initiatives, so we could reprioritize and continue with initiatives that had become more urgent and important and postpone what was not an immediate requirement or was no longer feasible.
We were able to continue our improvement ambitions at the same speed as before, if not more.
PEX Network: What trends do you expect to see in the continuous improvement space in the coming years?
VM: At present, organizations have a continuous improvement team that is expected to drive the improvement journey and come up with ideas. In the future, I see continuous improvement teams driving organizations by promoting an owner's mind-set with the entire leadership team across all functions in order to enable true commitment towards change. This change was already happening in the last five or 10 years, but I see it becoming more important in the future.
I also believe continuous improvement teams would evolve faster in adopting new methodologies and have a higher appetite for calculated risks. The technology we have now, the minimum viable product approach, AI, machine learning and data science are relevant today, but they will become commonly known terminologies in the future. I see organizations increasing their investment on digital products and services in order to stay relevant with the continuous improvement team having an important role to play in this transformation.
As Mark Twain said: “Continuous improvement is better than delayed perfection.” When it comes to minimum viable product, organizations need to acknowledge that. The journey is not going to be perfect and any changes will create disruption in the beginning. If organizations can put their heart into it, it is going to bring about positive differences.