Operational excellence challenges: 5 tips to overcome them
Experts from PEX Network’s top 50 thought leaders in operational excellence share their advice for overcoming business transformation challenges
Add bookmark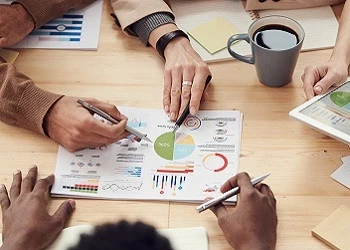
PEX Network recently launched its guide to the top 50 thought leaders in operational excellence for 2023, a group of people from all over the globe who have successfully led initiatives to help businesses transform and improve their processes, inspiring and leading others to do the same within their organizations.
Here we speak to seven of our top 50 experts who share the most common challenges they have seen companies struggle with when trying to achieve operational excellence, along with their advice for how to overcome these barriers.
Don't miss any news, updates or insider tips from PEX Network by getting them delivered to your inbox. Sign up to our newsletter and join our community of experts.
1. Embrace a culture of change and encourage others to follow
Damon Baker spent nine years at the Danaher Corporation, one of the first companies in North America to adopt Kaizen principles for its manufacturing processes. He has since founded consultancy firm Lean Focus and created the Lean Focus Business System, a problem-solving methodology that has been implemented by leading manufacturers around the world.
Baker explains that the biggest challenge he sees at organizations is fear of change, especially when trying to implement a Lean system. “Shifting to a Lean mindset requires a cultural transformation that may encounter resistance from employees who are comfortable with the status quo or fear the unknown. Overcoming this resistance and gaining buy-in at all levels of the organization is crucial for successful Lean implementation,” he says.
"If you are not making mistakes, it might be because you are not trying hard enough." Didier Rabino, Lean Management Systems.
Didier Rabino, instructor in Lean Certification Bronze and the president and owner of Lean Management Systems, has a similar viewpoint. “Leaders who are beginning to adopt Lean management may face challenges when it comes to adjusting to new mental models and routines, particularly if they differ from past successful practices,” he says.
Rabino cites the advice his coach once gave him: "’If you are not making mistakes, it might be because you are not trying hard enough.’ I realized that making mistakes can be a sign that you are pushing yourself and trying new things,” he adds. “I should not be afraid to step out of my comfort zone and embrace the occasional misstep as a valuable learning opportunity. I should keep striving for growth and improvement."
2. Drive change management with clear communications and collaboration
Alexis Nicole White has led major change management projects for Ericsson, AT&T and the Indiana State Department of Health. She is currently the strategic business transformation manager at Genuine Parts Company, an Atlanta-based business with almost 50,000 employees that distributes automotive replacement parts.
“As leaders, driving organizational change and transformation can be challenging, especially when it comes to securing buy-in from stakeholders, particularly executives,” White says. “Overcoming pre-existing beliefs that limit their ability to perceive such changes as sustainable is key to driving lasting transformation. That's why effective communication is crucial.”
"Sustaining long-term adoption and buy-in depends on making the change personal for execution teams." Alexis Nicole White, Genuine Parts Company.
Clear communications and collaboration are vital, she says, adding that “to ensure executive support and engagement from all parties involved, it's essential to present information in a transparent, step-by-step manner and encourage feedback loops.
“Collaboration is key to success, and having a small group of champions from all facets of the business can provide valuable insights into the impact of change on the workforce. Sustaining long-term adoption and buy-in depends on making the change personal for execution teams.
Answering the question, "What's in it for me?" can help stakeholders understand the benefits of the change. With the right communication strategy, we can overcome these challenges and drive significant organizational transformation.”
3. Explain why, what, and how you are transforming business processes
As the principal consultant of The Crysler Club, Dave Crysler draws from his years of experience working in manufacturing and distribution to advise others on ways to cut waste and achieve operational excellence.
“I believe the most common challenge is effectively communicating the vision,” he tells us. “This can show up in a variety of ways from general lack of stakeholder engagement to complete failure of a specific initiative or project.
“I recommend taking the approach of starting with and communicating the ‘why’ as well as the ‘what’ behind the vision before jumping into the ‘how’. Why are we wanting to make this change. What impact are we expecting to have. If these two things are communicated clearly and consistently, people are much more receptive and often contribute meaningfully to how the vision can ultimately be achieved.”
4. Model the change you want to see and lead by example
For Eric Lussier, principal at Next Level Partners, it is vital to set the tone at leadership level before implementing changes across the organization.
Lussier has been applying Lean and continuous improvement practices to almost all the company departments he has worked in for the last 25 years, including quality, human resources, sales, leadership and product development.
He says: “As a Theory Y leader, I get to choose how I view people and their contributions, and part of demonstrating the respect for the people principle of Lean and continuous improvement is being willing to listen and learn."
"The two most famous words from leaders should be ‘follow me’." Eric Lussier, Next Level Partners.
"That is why we as leaders must go see for ourselves first hand the challenges and opportunities to make improvements. Furthermore, we need to participate and model the behaviors desired including Kaizen participation on our own.”
Lussier adds, “The two most famous words from leaders should be “follow me”, where they are setting the example by being actively involved in the process and talking about the process-based changes that need to be made to enable the culture of continuous improvement to thrive.”
5. Avoid competing objectives and silos at all costs
Veronica Marquez was continuous improvement manager at L'Oréal and division manager in operational excellence for the city of Montreal, before founding Aristeo, a consultancy firm providing supply chain optimization and continuous improvement services.
Marquez says that the biggest challenge organizations face when trying to achieve operational excellence is overcoming silos. “The fractured management of businesses creates a dynamic in which each department has its own objectives to reach, sometimes even competing against other departments, and prevents developing a holistic view of the organization. This perpetuates the silo effect, which in turn causes lack of communication, lack of foresight, and slow reaction time.
“For operational excellence to be powerful, everyone needs to understand the clients’ needs, how the organization delivers on its promises, and what it can do to improve and innovate,” Marquez adds. “This approach will also help organizations reach an urgent level of commitment and devotion to improving our sustainability efforts, thus reducing our environmental impacts while improving our social and governance foundations.”
“Human intervention will be the key to creativity, innovation and solution finding.” Veronica Marquez, Aristeo.
With the increasing use of technology, Marquez believes that operational excellence will rely much more on human skills than on manufacturing processes. “A new formula or algorithm will eventually be developed and change these processes, but human intervention will be the key to creativity, innovation and solution finding.
“Operational excellence will have to become further integrated into an organization’s culture so that its vision is holistic, and it looks more toward reaching organizational excellence than to continuing to work on operational processes,” she says.
For Suzanne Rabicoff, head of new verticals at Invisible Technologies, siloed working is also the greatest challenge. The advocate of digital transformation and artificial intelligence (AI) says: “Potential risks organizations should be aware of when digitizing to pursue operational excellence largely stem from siloed decision-making with siloed data sets. To prevent wasting time and resources on major projects like the incorporation of AI, I recommend this piece to guide cross-functional collaboration.
“Also, if an organization's IT or data teams are still considered back-office, this is code red and leadership must move them front and center to protect the company.”
Further reading
- What is operational excellence?
- Why Lean Six Sigma is poised for a comeback in 2023
- An introduction to Gemba Kaizen
All Access: AI in PEX is 2025
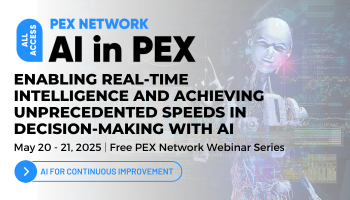
All Access: AI in PEX 2025 is designed to address these challenges and empower organizations to successfully integrate AI into their process improvement initiatives. The content series will bring together industry experts, thought leaders, and practitioners to share insights, best practices, and real-world case studies.
Register Now