Choose to maintain your business processes
Don’t wait for something to go wrong before you invest in process management
Add bookmark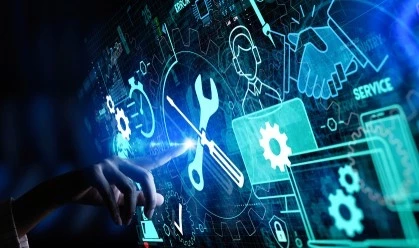
According to most major car manufacturers, you should service your vehicle every 7,500 miles or 12 months, whichever comes first. That may be as simple as an oil change and check of major components, or a more significant overhaul of various systems and parts. The routine is usually spelled out in a maintenance manual with scheduled work planned out in advance.
It’s recommended because those elements are all capable of failing, or suffering reduced efficiency, and that’s something you want to be aware of before it becomes a problem. Anyone who has invested in a new vehicle will tell you it’s better to identify potential problems and deal with them on your terms than have them come up on a highway, miles from home and when you’re not expecting it.
Don't miss any news, updates or insider tips from PEX Network by getting them delivered to your inbox. Sign up to our newsletter and join our community of experts.
The same is true for process management. Maintaining and fine-tuning business processes is a regular and vital part of ensuring operational stability. Continuous improvement needs to be a practical reality, not just a philosophical line in the company profile. Without it, businesses risk the same kinds of outcomes – issues that could range from frustrating to catastrophic. All of this should be captured in a practical and accessible process platform that keeps everyone, from process experts to on-the-ground teams, aligned on their role in effective process management.
Of course, we all know this, but it’s easy to postpone something slightly inconvenient, like preventative maintenance, when the need isn’t apparent – but that’s the best time to do it.
It’s running fine right now
Many businesses don’t see the value of documenting their processes and assessing their effectiveness while operations are ticking over as usual. When there is a profit being made and goals met, it’s difficult to justify allocating resources to examine the workings of the organization. It’s just like when a car is running smoothly; there’s little incentive to look under the hood. However, regular checkups are the best way to identify issues before they surface.
Allocating time and resources to process improvement is vital when the business is performing well. These conditions provide a safety net of effective operations to allow for examination and improvement of business processes. It lets teams and process experts alike consider, ‘if the status quo is good, what might better look like?’
Process improvement also allows an organization to plan improvements. An effective process platform serves the business by providing a framework to examine existing processes, working with the stakeholders to identify pain points and unmapped procedures and exploring solutions like automation. Process management can be timelined and managed to limit the impact on day-to-day operations while providing ongoing benefits as improvements come online. Like scheduling a car for a service, it happens when it’s most convenient – as long as it actually happens.
READ: Avoid assumptions when capturing your processes
When there’s a noise under the hood
The alternative is all too familiar for many companies. Critical issues can arise from numerous different sources. The COVID-19 pandemic created disastrous conditions for many organizations, with the ongoing financial impact of that period still felt by some. More localized events, from political changes to natural disasters, can quickly turn a smooth operation into a series of breakdowns and roadblocks. Even internally, unforeseen events like changes in staffing or unrecognized gaps in processes can suddenly create holdups or compliance problems that threaten ongoing success. Like an unexpected noise from the engine while on vacation, they’re unwelcome interruptions that demand attention at the worst time.
When things like this occur, the challenge is identifying the best ways to mitigate the damage and restore operational integrity. The path to success is remarkably similar to what it would be any other time – effective process management, clear documentation and the deployment of the right tools to achieve robust and efficient outcomes. However, it must be done to keep pace with the added pressure of skyrocketing costs, limited resources and compressed time pressures.
READ: Rebranding process excellence as process enablement
An ounce of prevention
Effective process management is preventative maintenance for businesses. It’s the oil change and new filters for an organization that help ensure costly breakdowns are less likely to happen when they’re least expected. By utilizing a collaborative and clear process platform and scheduling ongoing continuous improvement initiatives, a business can find peak efficiencies, rationalize costs and secure procedural weak points before they cause critical failures.
The freedom of resources available during smooth operations provides a backstop for the deliberate examination of processes and enables a strategic approach that reduces interruptions and the likelihood of major failures. Don’t wait for something to go wrong before you invest in your process management. Just like maintaining your vehicle’s maintenance, making continuous improvement the regular service schedule for your business will help ensure smooth operations for the road ahead.