8 brands using process intelligence to drive business value
Process intelligence is increasingly important for organizations seeking to gain a competitive advantage through process optimization
Add bookmarkListen to this content
Audio conversion provided by OpenAI
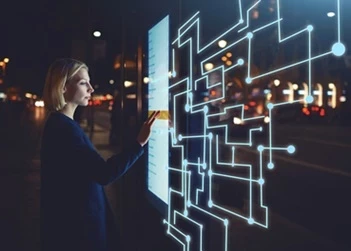
Process intelligence is a huge process excellence buzz phrase right now. This emerging, data and technology-driven approach to process optimization offers vast new opportunities for businesses seeking to gain a competitive advantage through process improvements.
With process intelligence, businesses access real-time data and predictive analytics, allowing them to make more informed decisions. This helps to support and enhance operational excellence (OPEX) and business transformation in more innovative ways – from accelerating automation and efficiency to reducing costs and improving compliance and governance strategies.
Here are eight brands using process intelligence to drive business value.
Don't miss any news, updates or insider tips from PEX Network by getting them delivered to your inbox. Sign up to our newsletter and join our community of experts.
Emerson
Global Fortune 500 company Emerson uses process intelligence to guide data-driven decisions on high value improvements. Emerson’s commitment to continuous improvement for the customer journey had meant using tools like Six Sigma and manual process mapping sessions. Rather than react to various reports and subjective information, the firm wanted to base improvements on what the actual data from the process indicated.
“ABBYY Process Intelligence has helped us make a real cultural change: to rely on data and make data-driven improvements,” says Simon Higgs, director of business transformation and optimization for measurement solutions. “The data doesn’t lie.”
With process intelligence, data can be viewed in “whole new ways” to drive value through the organization, conversations about process improvements and compliance are now data-driven and simulation of potential improvements saves time, effort and expense.
Siemens
Siemens’ IT team is using process intelligence to analyze data more accurately, react more quickly and uncover new opportunities. A storied organization with over 300,000 employees across 170 countries, Siemens is known for manufacturing, digital transformation and tech enablement. IT covers a broad portfolio of the company’s core processes and applications across many business areas, with data paramount to capabilities.
The IT team faced a gargantuan task: migrating everything to a cloud warehouse and, once there, finding and implementing improvement opportunities in processes and business capabilities. The ultimate goal was to use the cloud and process intelligence capabilities from Celonis to support Siemens’ business, increase efficiency and customer satisfaction.
Managing the project via a center of excellence (CoE), the overall migration to the cloud took about 18 months. Siemens stored data and created models in a domain structure within a cloud-agnostic platform, using Celonis as its front-end solution to visualize processes in near-real-time, get alerts and take action.
Process intelligence has enabled Siemens to transform processes in areas including supply chain resiliency, purchase-to-pay, inventory management and internal logistics and factories.
Teva Pharmaceuticals
Teva Pharmaceuticals, an Israeli multinational pharmaceutical company primarily known for its extensive generic drug portfolio, uses process intelligence to unify global operations. Teva needed to simplify a complex IT system landscape and standardize core business processes that differed due to growth by mergers and acquisitions across 60 countries and markets.
With process intelligence from SAP Signavio, Teva launched an end-to-end procure-to-pay process modeling and investigation project that spanned all systems and involved all business areas. It has also put business process management at the center of the program, connecting relevant elements and creating a complete and centralized view of business impact. Meanwhile, business analysts have been better enabled to discover and evaluate opportunities for improvement.
“We have accessible process modeling for everyone from the CEO and department managers all the way down to the end user,” says Haim Baruch, head of global business process management, center of excellence at Teva. “There is so much available, including trainings, tracking and comparisons. We now have one single source of business process truth for the company.”
Register for All Access: Revolution in Process Intelligence APAC 2025 to explore measuring the success of process intelligence initiatives
Smurfit Westrock
Smurfit Westrock, a leading sustainable packaging company, has successfully used artificial intelligence (AI) driven process intelligence to optimize inventory management. Smurfit Westrock faced challenges in mastering data inconsistencies, such as duplicate materials, language inconsistencies and synonym-based descriptions which resulted in unnecessary inventory buildup, procurement inefficiencies and higher costs.
Using the Celonis Process Intelligence Graph and large language model (LLM)-based analysis, Smurfit Westrock was able to harmonize its master data, creating a foundation for AI-driven inventory management.
Within just two months, Smurfit Westrock identified that many purchase orders were raised for spare parts that were already in stock. Additionally, a significant amount of spare parts had remained unused for over eight years.
“In August 2024, when one of our European plants had a breakdown, the supplier quoted us a significant delay for the supply of a replacement part,” says Brian Dodson, business process improvement manager at Smurfit Westrock. “With Celonis, we were able to find a plant in the region with the needed part and schedule a transfer order in under a day. This enables us to unlock new levels of efficiency, deliver enhanced value to our maintenance teams and drive sustainability.”
Finlay’s
Finlay’s, a global supplier of tea, coffee and botanical ingredients and solutions to many of the world’s beverage brands, retailers and foodservice operators, is using process intelligence to enhance supply chain visibility, streamline operations and elevate customer service while reducing costs and supporting continuous improvement.
In partnership with QAD, Finlays aims to utilize real-time, data-driven insights to enhance visibility into its supply chain, enabling greater business transparency and eliminating the inefficiencies inherent to processes designed around assumption-based models.
“As a company with a long heritage, we recognize the importance of innovation to stay competitive in today’s dynamic supply chain landscape,” comments a Finlays representative. “QAD Process Intelligence will enable us to make data-backed decisions that enhance efficiency, improve supplier management and deliver better service to our customers.”
netgo
netgo, one of Germany’s 20 largest IT solutions providers, is using Nintex Process Intelligence as a centralized, adaptable platform that manages processes across the organization, enhancing visibility and enabling regulatory compliance tracking via ISO certification. After acquiring three to five companies annually for a number of years, netgo needed to integrate many different corporate cultures and processes while remaining compliant and continuing to prioritize growth.
Process intelligence has provided netgo with the capabilities to map, share, assess and optimize its sales processes across teams. Automated workflows ensure both new and existing employees adhere to essential sales processes, affording a clear, transparent view of roles and processes.
It’s also helped the firm streamline, document and communicate processes throughout its operations, simplifying the ISO certification process and allowing for clearer oversight and easy updates. “Securing ISO certifications becomes more efficient and cost-effective as everything is methodically organized,” says Andreas Rohde, compliance officer and head of integrated management systems at netgo. “There’s no need to sift through old documents for evidence – it’s all readily available.”
What’s more, Netgo integrated process intelligence capabilities into other operational workflows and has seen improvements across the board. With netgo employee onboarding, for example, newly structured process saves time for new hires and management alike, while significantly reducing paperwork errors.
Download The power of process intelligence: 2024 industry report
Zespri
Zespri, the world’s leading marketer of kiwifruit, has delivered millions in value by optimizing operations with process intelligence. In collaboration Celonis, Zespri embarked on Project Horizon, an ambitious multiple-year effort to transform the company’s processes and systems.
“When we started to analyze our data in the Celonis Process Intelligence platform, we saw the immediate opportunity to improve our procurement and purchase-to-pay processes,” says Dave Scullin, chief digital officer of Zespri. “Celonis has been instrumental in enhancing our processes at Zespri helping us to drive better outcomes for our people and our customers and more value for our growers.”
In just 18 months, the Zespri team has been able to achieve:
- A 27 percent reduction to its vendor invoice management (VIM) cycle time.
- A 23 percent increase in purchase order conformance.
- A 68-day credit memo clearance improvement.
- Identification and prevention of potential duplicate spend.
Iris Bank
Iris Bank, a financial institution that provides a wide range of banking services to individuals and businesses, uses process intelligence to improve operational efficiency, streamline processes and identify areas for automation within its daily operations.
It applies ProcessMaker’s process intelligence tool to analyze various team activities, identify inefficiencies and provide actionable insights that have led to significant time and cost savings.
The main objectives include:
- Understanding the existing processes within Iris Bank’s operational and commercial teams.
- Identifying process bottlenecks and variance in productivity.
- Uncovering unused licenses and opportunities for automation.
- Standardizing processes for consistency and efficiency improvements.
By streamlining manual data transfer processes through automation and minimizing process variation in certificate of deposit (CDT), Iris Bank achieves substantial efficiency gains, identifies areas for cost savings and explores opportunities to optimize processes through automation.
PEX Report 2024 global state of process excellence
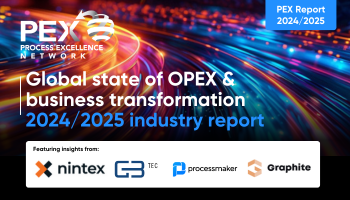
PEX Network's annual report reveals the current state and future trends of process excellence. Based on a study profiling hundreds of global process excellence leaders, the report provides insights on how to leverage innovation, generative AI, and process intelligence to achieve operational excellence, customer-centricity, and organizational growth. Download your copy of the PEX Report 2024/2025 today and benchmark your process excellence journey against your peers.
Download Now