What process mining can’t do: Why Fortune 500s are choosing task mining instead
Learn why process excellence leaders are passing on process mining in favor of task mining
Add bookmarkListen to this content
Audio conversion provided by OpenAI
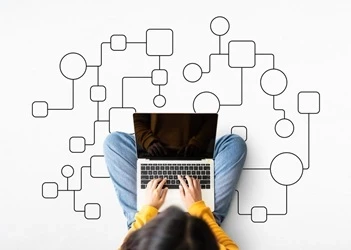
With every earnings cycle, another Fortune 500 company announces a massive cost-cutting initiative. Behind the headlines, chief financial officers (CFOs) and operations leaders are under mounting pressure to drive efficiency without sacrificing performance. In conversations with these executives, one question keeps coming up: How can AI-powered process intelligence help teams do more with less?
Until recently, process excellence leaders have relied on process mining to analyze workflows. However, a growing number of enterprises are realizing its limitations. While process mining reveals system-level bottlenecks, it misses the key human actions that create real inefficiencies. Task mining fills this gap. By capturing and categorizing employee actions into detailed process maps, task mining shows exactly how to streamline, standardize and automate processes across the entire organization.
Why process excellence leaders are passing on process mining
Process mining can analyze system logs and tell you that a bottleneck exists, but it can’t tell you why. In an enterprise where thousands of workers may complete work step-by-step manually, a lack of desktop-level insights makes it impossible to successfully improve processes. Task mining captures the full end-to-end workflow across all desktop applications – including clicks, keystrokes and actions — identifying issues with people, processes and underlying systems that are the root cause of bottlenecks.
Process mining also takes time – it can take six months or more for a single process to be mapped and analyzed due to a long setup time, significant data preparation required and the need for additional engineers, specialized business analysts or external consultants to implement the solution and interpret the data. On the other hand, within a couple of weeks, AI-powered task mining can map the full scope of work being done in a process and provide actionable recommendations for process improvement and automation, without the need to prepare data, implement on-premise solutions or hire additional consultants.
Simply put, task mining looks at what people actually do on their computers and then uses that data – also known as process intelligence – to find new ways to automate tasks, make work easier for employees, help them get more done and make the case for implementing generative AI.
Task mining gets results for Fortune 500 companies
Fortune 500 transformation initiatives are successful with task mining because it shows exactly how the team works, then suggests wasteful activities to eliminate, recommends opportunities for AI and automation and continuously measures productivity and conformance. Here are some real examples of F500 enterprises – with substantial process mining investments – who found and realized the value of task mining over process mining.
- F500 tire manufacturer optimized their payroll ticketing process. Task mining identified that the payroll ticketing team spent over 50 percent of their time in spreadsheets and that enterprise resource planning (ERP) was not optimized for most ticket types, resulting in workarounds and avoidable data entry. Rebuilding the requirements for the ERP based on task mining’s recommendations resulted in an 80 percent reduction in manual work.
- F500 car rental company reduced customer call time on rental extensions. Task mining discovered that contact center agents spent the majority of their time looking up reservations in customer relationship management (CRM) while manually performing cost estimates on rental extensions in a spreadsheet. By updating the software to automatically load reservations from call-in phone numbers and generate estimates, rental extension call time was reduced by 31 percent.
- F100 biotechnology company transformed their customer service function. Task mining confirmed the suspicions of this team that most of their contact center agents’ work was done outside of ERP, and that call volumes were negatively affected as a result. The resulting recommendations for upstream process improvement, automation and AI initiatives increased the volume of calls that each agent could handle, allowing fewer agents to better handle the same volume.
- F100 pharmaceutical company improved their month-end close process. Task mining identified hundreds of tasks being performed by Merck’s Account-to-Report (AtR) team, then made suggestions for elimination of unnecessary tasks and automation of others, which achieved 20 percent of the total GBS cost reduction annual target in a single month.
Task mining discovers every process improvement and automation opportunity that exists. The above success stories alone represent thousands of hours of work and millions of dollars of savings which process mining missed. It’s easier to build a comprehensive picture from granular data on the entire enterprise than it is to build that picture from data pieced together from discrete systems. This is where task mining shines and it’s why task mining will subsume the process mining market in the near future.
Don’t miss the opportunity to learn how Merck uses task mining to diagnose and solve hidden inefficiencies missed by process mining. Steve Carpenter, head of GBS Digital Services at Merck recently joined the PEX Network’s All Access: Process Intelligence and Process Mining 2025 webinar series and you can now watch his session on demand.