A guide to process simulation
Discover what process simulation is, how to conduct it and how it helps companies navigate new markets
Add bookmarkListen to this content
Audio conversion provided by OpenAI
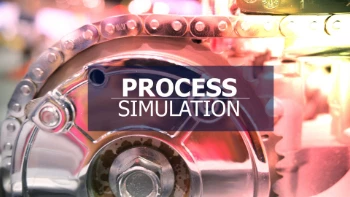
Organizations need to create flexible long-term plans with a culture of changing mind-sets due to a number of factors. These include the evolution of complex and surprising innovative and disruptive future business models, a constant impetus to focus on economic progression and the consumerization of technology such as the five digital forces – mobility, Big Data, social media, cloud computing and artificial intelligence.
Organizations can do this by performing scenario planning and analysis. While doing so, simulation of future predictable and unpredictable outcomes of such strategic business scenarios becomes vital to perform a “reality check”.
This guide describes business scenario simulation using “business process simulation” as a lever to unravel a structured methodology for simulation. This will help organizations define, analyze, improve and imbibe future to-be business processes.
Organizations can assess and manage change by focusing on business process patterns, modeling process flows, carrying out design of experiments and analyzing factor-based scenarios. Business process simulation is a widely used phenomenon in process modeling as well as process mining.
What is process simulation?
Simulators are used by companies worldwide for various business needs. These include business scenario management where they input variables into the simulator and decide whether the problem can be solved within the bounds of physical reality, time and cost constraints. Simulators also help in scenario development and business model analysis.
Whenever a company decides to pursue technological transformation, an expected return on investment (ROI) is always kept as a benchmark.
Business process simulation provides a mechanism for robust validation under realistic conditions and if the simulator’s outcomes are not in sync with the expected results, it can substantially reduce the risk of deploying a new process.
Simulators allow businesses to dynamically examine process flows, validate the model and collect timing and resource information on proposed or legacy processes with a view to improve them.
Based on the results churned out of the simulator, companies can take a call on whether it is worth continuing with legacy systems, such as mainframes, or opting for a new technology implementation.
Related article: Why the real value of process mining lies in simulation
Simulators perform a “reality check” before conducting costly system implementations by simulating the what-if scenarios against as-is or other statistics-based process models. This helps companies understand how the to-be system will respond in reaction to changes or fluctuations of certain environment or system parameters.
Based on this logic, companies simulate processes to ensure strategic alignment in merger and acquisition scenarios, the implementation of new product or service lines, or ventures into new geographies.
Related article: How Danaher achieved an annual 30 percent growth with an effective acquisition strategy
Simulators also provide insights into alternate process flows, suggest course corrections, help reduce defects and increase customer satisfaction. They are used to assess the development of process and resource performance over the course of time.
Resource performance looks into the softer aspects of the process such as the people involved, bottlenecks occurring due to dependencies and idle time. The simulation results provide insights that support decisions in process design or resource provision with the goal to improve factors such as process performance, process and product quality, customer satisfaction and resource utilization.
Below is a step-by-step outline of a process simulation project:
- Trial run the options being implemented or suggested for the process to be run in the real world
- Examine the consumption patterns of workforce and devices used throughout the process
- Identify business-specific bottlenecks and optimization of the company’s business processes
- Analyze workload and sufficiency of resources available to the process
- Estimate the efficiency of business process improvements
- Conduct risk assessment, risk minimization and risk control
The different elements of process simulation
Adding inputs
Modeling is a necessary component of any simulation. The input for business process simulation, known as the simulation model, typically comprises information about process flow, resources and process instantiation.
The process flow defines the time-based and logical order of function execution. Further information is added to define the behavior of decision points or loops in the flow during simulation. In addition, the time spent for the execution of each function is specified.
One of the limiting factors in process execution is the availability of human and technical resources required to carry out the functions in a process. For these resources, an assignment to functions is made and is defined how many are required and provided.
Depending on the sophistication of the business process simulation, additional information can be given that include times of availability, failure rates or skills and capabilities.
Process instantiation patterns define when and how often a process is triggered. They represent the occurrence of events that trigger a process or the demand for process execution, for example by customers. Process instantiations might also assign properties to process instances which are relevant for decision-making further along in process flow.
Conducting design of experiments
Design of experiments (DOE) is used to figure out the relationship between factors that affect a process and the output of that process. DOE technique has been used to structure and organize simulation experiments.
These methods are step-by-step instructions for formulating a simulation study and for evaluating the results to demonstrate statistical significance. Some software tools provide guidance in setting up and running simulations within a DOE framework.
The first step is to define the business problem. While this does not require an understanding of the software tools, knowledge of process modeling and simulation are mandatory. The definition of the business problems is essential and directly determines the model parameters that will be varied, and the model metrics that will be analyzed.
Related article: Top three pre-process transformation actions to ensure success
The subsequent steps are process modeling and feeding inputs to the process simulator to generate results with multiple iterations for a specific scenario. In the end, businesses get a summarized result in the form of an Excel sheet or xml.
Companies can keep feeding different input values into the simulator until the identified problem is properly defined. A solid DOE minimizes the modelling and simulation effort and adds robustness to the results.
Based on the results derived from the simulator, the business analysts and process consultants can take a call on whether the company should go for the new process or not. If a methodical approach is followed to design and simulate the process, they will be able to answer questions regarding process bottlenecks and low-hanging fruits. They will also be able to determine where the focus should be to avoid any future pitfalls during the adoption roadmap.
How to perform process simulation
In order to perform process simulation using any business process model and notation tool, companies need to answer these basic questions:
- What is the expected time of completion for a specific process?
- What is the processing time per function?
- What are the probabilities of conducting a task in different ways?
- How many resources will be available to undertake the process?
- What is the workload of each resource?
- What are any ad-hoc interruptions that might occur?
The more pointed questions companies have, the more the accuracy of the simulation exercise will be. Most of the questions fed into the simulator are time-related and a few questions have weights assigned to them.
For example, a high-priority task has a weight of 10 while a low-priority one might have a weight of two. The results generated by the simulator entirely depend on values keyed into the simulator by the user.
Real-life example of process simulation
Let’s take a real-life example. A client asks you the following problem statement:
What distribution center network, including order management policies and replenishment strategies, are required to ensure profitability and maintain a 95 percent on-time performance for delivery of chip sets to global customers assuming a maximum 20 percent forecast (in)accuracy?
The text in bold identifies input variables or parameters that we can change in a simulation model and the text in italics identifies output metrics that are observed to determine the impact of the changes.
All these values will be fed into the simulator. The factors that can be changed are termed as controllable input factors in DOE terminology and the parameters that cannot be changed are termed as uncontrollable input factors.
The bold text values will keep changing for different iterations and the results generated out of these iterations will be displayed once the simulator completes the execution cycle. Based on the results generated, one can easily figure out the best combination of numbers which will give the desired result. In our case, the desired result will be the values displayed in italics above.
Analyzing process simulation results
The results of business process simulation comprise quantitative, time-based and cost-related information about process execution and resource usage such as waiting times, throughput times, completed process instances, resource utilization or cost per instance.
Another important output from the simulation experiments is standard deviation which can be used to identify the most optimal process.
Capacity utilization that includes people performing the tasks, possible bottlenecks, dependencies and idle times, can be analyzed based on the results available from the simulations. This data can be aggregated for the different model objects but also given per instance.
Related interview: Why data literacy is critical for process mining
For the analysis it can be interesting to evaluate the data at a certain point in time. This can be the number of completed process instances at the end of the simulation time or over time, for example the development of waiting times after a peak in demand.
This type of specific data can be generated by simulation and its analysis depends on the company’s goal for the simulation.
Conclusion
Process simulation is used to assess the health of an existing process and is widely used across the industry spectrum to identify bottlenecks and optimize the current business processes.
It also helps companies implement new business processes or adapting to a new technical environment in a merger and acquisition scenario and facilitates ventures into new geographies or untried and untested technical space. It rewards quantifiable benefits by performing logical analysis of the existing process models.
Various References for the research: www.pega.com, www.ariscommunity.com, www.simul8.com, www.isixsigma.com, pubs.opengroup.org, Modeling & Simulation in BPM - M. W. Barnett.
Do you leverage process simulation in your organization? Let us know by leaving a comment below.