How Merck uses task mining to uncover inefficiencies & automation opportunities
Task mining has enhanced Merck’s ability to identify the root causes of process issues
Add bookmarkListen to this content
Audio conversion provided by OpenAI
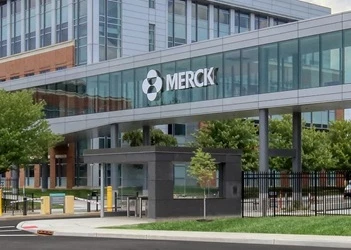
Science and technology company Merck is using task mining to uncover inefficiencies and identify automation opportunities as part of an ambitious transformation project.
Speaking at All Access: Process Intelligence and Process Mining, Steve Carpenter, Merck’s executive director, GBS digital services, revealed how task mining is helping the organization reclaim thousands of team hours and identify high-impact potential for automating processes.
Don't miss any news, updates or insider tips from PEX Network by getting them delivered to your inbox. Sign up to our newsletter and join our community of experts.
What is task mining?
Task mining captures and categorizes employee actions into detailed process maps, enabling teams to streamline and standardize workflows. In its simplest definition, task mining looks at what people do on their computers and then uses that data to find new ways to automate tasks, make work easier for employees, help them get more done and make the case for implementing new technologies such as generative AI.
Traditionally, process excellence leaders have relied on process mining to analyze workflows. However, a growing number of enterprises are realizing its limitations. While process mining reveals system-level bottlenecks, it misses the key human actions that create real inefficiencies. Task mining fills this gap.
Why Merck used task mining
“There are a lot of activities that happen in our processes that are inside an ERP [enterprise resource planning] system, but there is also a lot of stuff that doesn’t happen inside the ERP system,” said Carpenter.
This creates challenges, because while process mining provides valuable insight on how processes work within a system like ERP, Merck was struggling to access insight on non-ERP processes such as those that are less transactional – e.g. planning and forecasting, Carpenter explained. Even highly transactional processes inside ERP with long wait times between certain steps generated visibility issues, he added.
“That’s why we really started to look at task mining as the capability to bring in and help us understand that ‘white space,’” Carpenter said. Before adopting task mining, Merck’s approach to process optimization was dated and incomplete, he added. This involved engaging with high-cost consultants to perform value stream mapping, identify Kaizens and make incremental improvements as the firm went.
Identifying the root cause of process issues
Task mining has enhanced Merck’s ability to identify the root causes of process issues. “We probably have close to 40 digital twins in our process mining tool, which is very helpful and very useful. However, if there’s a gap in the process – if the users go off and do something in Excel or Outlook, and it takes hours to get back into the ERP to take the next step – the question is: Why?”
This is where Merck has used task mining to “really dig into some of those areas,” Carpenter said. “We’re looking at what happens when people are responding to incidents and service tickets within our ServiceNow solution [for example]. One of the things we’re thinking about doing is using Mimica [task mining] to dig into how workers are using ServiceNow and what they are doing outside of ServiceNow to get ready and prepare to answer questions or resolve incidents.”
Debunking common misconceptions
A common misconception is that task mining is limited to certain tasks, but it can be used to map entire, end-to-end processes at the click and keystroke level. “The first thing we wanted to do was really get into processes actually happening on the desktop,” Carpenter said. The key goal is to know exactly what is occurring to decide if steps can be eliminated, rework loops can be reduced and bottlenecks can be removed to eventually digitalize or automate part or all of a process, he added.
Another misconception is that it takes several months to identify high impact process improvement opportunities and act on them. However, Merck was able to start seeing process insight results within a week of applying task mining, according to Carpenter. “We decided which ones we wanted to really dig into, and put them into the mapper tool, which came back in another week or two. So, it was pretty quick.”
Identifying and prioritizing quick wins
Identifying and prioritizing quick wins is an important element of process optimization. Before task mining, Merck relied on process mining, which can only discover certain quick wins among specific processes.
By digging into processes at the desktop level, Merck can gauge how automatable a process is as well as how easy it would be to automate it, Carpenter said. “It really identifies those tasks that are happening most frequently and that take up the most manual effort.”
Merck ran an experiment by taking a process design document (PDD) from its task mining solution and fed it into a generative AI tool to create some Microsoft Power Automate code. “Within minutes, we had a prototype of a Power Automate bot that we could use to actually automate the task we had seen.”
Optimizing seasonality and certification processes
Optimizing seasonality processes – specifically monthly “close the books” processes – is one example of Merck benefitting from task mining, Carpenter said. “What we realized is that we could start to standardize and harmonize our teams to really complement each other in terms of the seasonality of one process versus the seasonality of another – combining that activity together so we could do it with less manual work.”
Merck also discovered certification enhancement opportunities. “In our certification process during close the books, we do a lot of commentary,” outlining what results mean and how they differ from previous quarters, Carpenter said. Merck identified a specific automation/AI opportunity with greater detail on the potential return on investment (ROI) based on various insights such as time spent on the commentary process.
Maintaining automation and AI-driven value
Maintaining automation and AI-driven improvements is a key factor in driving long-term value. Merck continually assesses automation rate, rework rate, cycle time, quality improvements and user experience through a “control tower” view of its process key performance indicators (KPIs).
“We would typically take a look at how a process KPI started up and how, overtime, it improved or didn’t – adjusting from there to try and figure out how we go after the original value we were targeting.”
Watch the full session with Merck featuring Tuhin Chakraborty, CEO of Mimica, on-demand now!
All Access: Business Transformation 2025
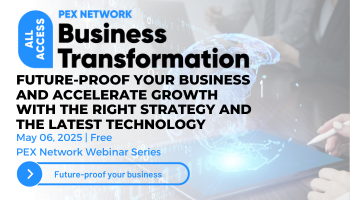
Don’t miss this opportunity to connect with your peers, gain exclusive insights, and future-proof your business. Join us at All Access: Business Transformation to future-proof your business and accelerate growth with the right strategy and the latest technology
Register Now