Why it may be time to change what you have always done
Discover how to overcome the status quo and eliminate inefficient, legacy processes by questioning the why behind organizational procedures
Add bookmark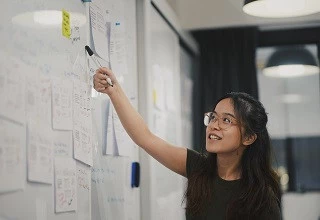
Grace Murray Hopper was a rear admiral in the US Navy and a pioneer in computer programming. She worked on the Harvard Mark 1 computer during World War 2 and laid the foundation for the programming language COBOL which is still in use today.
Amongst her many significant contributions to computer science, this quote from 1976 stands out: “The most dangerous phrase a data processing manager can use is, ‘we have always done it that way.’”
Nearly 50 years later, that statement rings true for business process managers too.
Process management relies on the drive to analyze the what and why of procedures and practices. It looks for waste and redundancies and explores the step-by-step motions of business activities for opportunities to create greater efficiency and effectiveness.
Continuous improvement is the antithesis of ‘we’ve always done it that way,’ and strives to replace the status quo with faster, more robust and more productive approaches.
But we still need to consider how to improve those phases between those highly optimized processes.
Process handoffs are often an overlooked aspect of operations but are key to the overall effectiveness of a business. The artifacts that come out of one process and feed into the next are seldom examined with the same rigor as the steps used to produce them. Yet they consume significant energy and effort, resources that are not always warranted.
Whether processes are linked by dependencies, or are procedurally sequential, when the outputs of one process serve as inputs for another they need just as much review as the steps they are intended to support or flow from.
Eliminate habitual activities that do not add value
Process stakeholders are a great place to start when you are taking stock. They are often the consumers of process reports or deliverables in one form or another – or they should be. Begin by checking what actually gets used.
While a monthly report may be mandated, how much of that data is used for anything besides creating another report? Which data points add value to the process in question, and which have lost their relevance with the growth of the business? How is the content used to influence decision-making within the process or related processes?
Consider each input and where that contributes to the process execution. If there is not a clear business value to it, trace it backward and see if it can be eliminated or recaptured in a way that does offer benefits.
Question the why behind your endeavors
When tracing back, each artifact should be examined on its merits. Producing reports and statistics is important for measuring effectiveness and capturing operational outcomes, but if those figures serve no value besides fulfilling an expectation for paperwork, they probably represent a wasted resource.
A famous experiment in the 1960s had a small troop of chimps sprayed with water when any of them tried to climb a ladder to reach a tantalizing banana. Once they learned the consequences of climbing, they stopped. When a new chimp was introduced, of course it tried to climb the ladder, but was swiftly pulled back by the others.
One by one, the chimps were replaced by new primates who had never experienced the water spray until none of the originals remained. However, because of the group conditioning, none of them dared to climb the ladder even though none of them likely understood why.
If no one in your organization can articulate why they are producing an artifact, and there is no clear reason for it to continue to exist, it is probably time to retire it gracefully.
It is easy for business operations to get bogged down by reports and metrics that have a long legacy but little value in the daily functions of the company.
These outputs and inputs need as much attention as the processes they flow to and from and they can represent significant amounts of time and energy for your teams that could be better directed to more meaningful artifacts.
In the spirit of continuous improvement, “we have always done it that way” is too dangerous a reason to leave old habits unexamined.
Has your business been guilty of perpetuating inefficient legacy processes? Let us know in the comments below.