Gemba Kaizen examples: 3 case studies outside manufacturing
While Gemba Kaizen originated in the manufacturing sector, the Japanese concept is now being applied in a number of different industries to drive continuous improvement
Add bookmark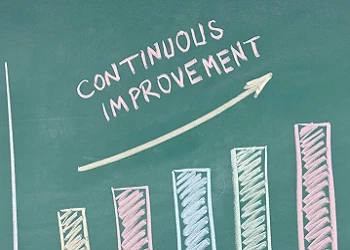
Gemba Kaizen is a business concept rooted in continuous improvement. The word Gemba translates as ‘the actual place’ from Japanese; while Kaizen means ‘improvements’.
The methodology originated in the manufacturing sector in the post-World War II period, originally developed to improve processes, reduce waste and enhance overall efficiency on the factory floor.
While it is still a popular approach in this industry (see the examples here), its key principles are versatile enough to be applicable across a wide range of fields, and its emphasis on a more efficient use of resources and eliminating waste make it highly relevant to businesses operating today.
Below we take a look at some examples of Gemba Kaizen principles in action being applied outside of manufacturing.
Don't miss any news, updates or insider tips from PEX Network by getting them delivered to your inbox. Sign up to our newsletter and join our community of experts.
Gemba Kaizen in schools and academia
Schools can apply Gemba Kaizen to improve the teaching environment in the classroom and streamline administrative processes like enrolment. In academic institutions, it can be utilized to improve research methodologies.
The Singapore Management University (SMU) Libraries has approximately 60,000 print items and 400,000 electronic resources across two locations. In 2013, the library embarked on a project to identify problems and eliminate waste in its ‘lifestyle’ print collection, which includes contemporary bestsellers, award-winning fiction, self-help books and travel guides.
As the lifestyle collection occupied a prime location within the library spaces, it was important to library management that the collection was visually appealing and accessible to users.
Using various metrics, the library team drew up a scorecard with key areas to monitor, including whether there were duplicate titles, the age and condition of the materials, whether the display was attractive to users and whether the subject matter of the books aligned to the library’s policy.
To assess this, library staff carried out a Gemba walk, a common activity in manufacturing factories, here adapted as a walkthrough of the libraries to report on each of the factors noted on the scorecard.
As a result of this exercise, staff were able to identify areas where the collection was falling short and apply suitable remedies, such as finding books with faded and damaged labels and either repairing or replacing these, as well as amending incorrect labelling of shelves which made it hard for users to find books. The walkthrough also led to the creation of new categories to help users find titles and attract more browsing.
Following this, quarterly Gemba Kaizen assessments were implemented which showed continuous improvements in the areas indicated on the scorecard.
Transforming daily meetings in the pharmaceutical sector
At one well-established pharmaceutical company, daily production meetings had become time-consuming and were no longer focused on the needs of the company. The business decided to use Gemba Kaizen to re-center the meetings around organizational goals and improve communication.
It did this by introducing short 15-minute stand-up meetings at the start of each day attended by leadership, maintenance, quality and engineering representatives from different teams. The meetings have a clear, structured agenda, starting with customer-related areas and moving to health and safety, quality concerns and reviews of different projects.
Issues, actions and suggestions arising from these discussions are documented on action cards, removing the need for minute-taking. Card owners are held accountable for providing regular status updates, ensuring progress towards identified goals. Later in the day, members of senior management meet for an update following the same meeting format.
Adopting this approach has led to more focused meetings aligned to the company’s objectives, better collaboration between teams and a greater sense among staff members of operational challenges, enabling them to be proactive about issues before they escalate.
Using the 5S of Gemba Kaizen in food production
From production to distribution and retail, the food and beverage industry can benefit from Gemba Kaizen to improve food safety, quality control and operational efficiency.
At Trapiche, an artisan mill in north central Colombia that processes a type of cane sugar called panela, the 5S principles of Gemba Kaizen led to a number of efficiencies in productivity.
Most of the operations at the mill are performed manually, so the goal was to tidy and clean workspaces to create a more productive work environment. The 5S (sort, straighten, scrub, systematize and standardize) is a housekeeping technique used to organize the workspace in a clean, efficient and safe way.
First, necessary and unnecessary elements were classified in each workplace with red and green cards respectively, after which all unnecessary items were removed and necessary items were organized by location, name and volume. Among the changes made was installing an organized tool board so that operators can easily find the tools they need and return them once no longer in use.
Next, an order and cleanliness program was created to keep the facilities clean and eliminate sources of dirt. This was promoted with laminated infographics of how workstations, machines and tools should be kept, with safety and cleaning instructions. An auditing checklist was also created for each person’s role, to foster a culture of self-discipline.
Implementing this program has helped prevent accidents, reduce the time spent searching for tools and avoid product contamination, overall leading to an improvement in order and cleanliness of 63 percent.
All Access: AI in PEX is 2025
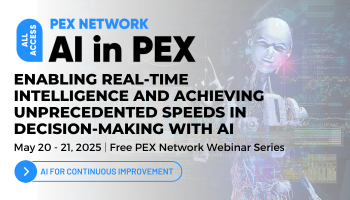
All Access: AI in PEX 2025 is designed to address these challenges and empower organizations to successfully integrate AI into their process improvement initiatives. The content series will bring together industry experts, thought leaders, and practitioners to share insights, best practices, and real-world case studies.
Register Now