Organization maintenance culture: Laying the groundwork
How to achieve a safe, predictable and reliable organization
Add bookmark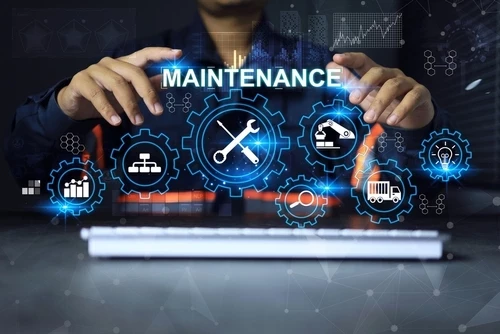
From documentation discrepancies to non-standard maintenance practices to plant shutdown – how did we get here? From the perspective of a veteran maintenance manager, the previous chain of events would capture my attention. The span of responsibility in the maintenance role can be quite intimidating to any maintenance manager. To the experienced ones, oftentimes we find ourselves in a comfort zone or false sense of security when our systems, subsystems and utilities are all online with minimal backlog and maximum uptime.
We might become even more content when operations are hitting goals, packaging and shipping ar busy sending out products while the quality department are at idle with reports and investigations. Enter the “Swiss Cheese Model,” credited to James Reason in 1991 in his book Human Error. He asserts that accidents and failures are typically not credited to just one or more independent events, rather they are linked to multiple issues occurring in isolation overtime and eventually lead to a catastrophic result. Such is the case with the following scenario adapted from an actual situation in a leading pharmaceutical manufacturing organization.
Don't miss any news, updates or insider tips from PEX Network by getting them delivered to your inbox. Sign up to our newsletter and join our community of experts.
Pinpointing failure
Imagine getting a text and then a phone call in the early hours on a Saturday morning indicating a major piece of machinery has failed and stopped production on the most critical line. Even worse, the failure has caused the rejection of products, causing a loss exceeding six figures. The equipment train at the facility is comprised of large-scale, high-volume compressors, chillers, vacuum pumps, steam generation and mixers. Boilers, instrumentation, automation, centrifugal pumps, electrical distribution, all inter-connected through piping, flanges, valves, manifolds, heat exchangers and so on, have limitless possibilities of failure modes. For the technicians and engineers, it can become challenging to pinpoint a failure that has indicators in one area yet a root cause in another. As we delved into the symptoms of failure, it seemed obvious at first, but then the deeper we dug, the more complex it became until the solution(s) seemed unattainable.
Small, seemingly insignificant actions slowly infect a culture
Over time, a series of events laid the groundwork for the catastrophic failure of this particular event. There were events in the past where a pump would fail, a refrigeration leak would occur, a thermocouple would not read accurately, an electric motor would indicate vibration, a machine guard was removed and not reinstalled – the list goes on and on. We could even cite the change of leadership, staffing challenges, high turnover and many other factors such as varying techniques in performing tasks.
These small, seemingly insignificant actions slowly infected the culture and became the norm by accepting maintenance practices that did not meet industry standards. Couple that with the documentation process of work orders such that little information was available to go back and reference resulting in a lack of critical data points in terms of operating hours, clearances, pressure, temperature, torque, belt tension and many other factors. These issues were difficult to spot for the untrained eye; even more difficult to spot for the current employees as they walked past these discrepancies’ day in and day out.
Quick fixes, cutting corners, missing/broken fasteners, loose hardware and oily residue all became commonplace. To recover from this and then restore and sustain, a rapid, reliable and proven series of tools and methodologies was in order. Historically speaking, these types of failures and violations are more common than you might think. Numerous examples of citations from Title 21 point to common threads such as poor or lack of documentation, not following standard operating procedures (SOPs), inability to demonstrate RCA and so on. From a maintenance management perspective here are some concepts that can provide critical insight to assessing an organizations maintenance culture, implementing best practices and laying the framework to reliability to achieve a safe, predictable and reliable organization and following CGMPs.
READ: Choose to maintain your business processes
It all starts with safety
The environment, health and safety (EHS) department and staff play a critical role in an organization. They are the pinnacle of a culture of safety and are the driving force of mishap prevention. With Occupational Safety and Health Administration (OSHA) compliance and personnel safety as the top priorities, the EHS staff can be infinitely beneficial by working closely with the maintenance personnel to promote a safe, predictable and reliable culture. Frequently inviting them into the maintenance shops and machinery areas promotes clear and open dialogue between technicians and EHS by providing a fresh perspective to identify discrepancies or to take action before a hazardous situation arises.
They have an abundance of resources as well as a dedicated budget to enhance the work area in the terms of ergonomics, effective lighting and labeling as well as providing necessary equipment to enable the technicians to do their job at a higher level. In addition. They are the SMEs in areas of LOTO, HAZMAT, fall protection, hearing conservation, pollution abatement and many more areas.
Leaders work closely with EHS to develop localized checklists, schedule CPR, respirator, spill prevention and recovery and scores of other training topics. EHS personnel should always be welcome and be an ear to receive suggestions as well as give feedback to ensure not only does everyone go home with all their fingers and toes at the end of the day but makes the workspace clean and safe. A best practice of a maintenance manager is to appoint one or more of the team (depending on size) as a safety representative to work closely with EHS personnel and act as a liaison between the two entities. Moreover, incorporating a weekly five-minute safety topic can enhance awareness, education and make safety a common culture throughout the organization. Taking it to the next level, EHS personnel can promote a culture of safety by implementing an awards-based system to highlight areas of success with specific examples, documenting and publishing statistics and then focusing training on targeted areas.
Achieving an elevated level of predictability
To achieve an elevated level of predictability, maintenance leaders should adopt and enforce the concept of “leave it better than you found it.” This notion implies a sense of pride to be instilled in the team which translates directly to equipment and process predictability. One of these concepts is referred to as the “Broken Windows Theory” introduced by James Wilson and George Kelling. Does the phrase “somebody should take care of that” sound familiar? When in the break room, does a discussion come up about a problem area but no one claims ownership of it? With the concept of broken windows, it starts with one small discrepancy that gets continuously ignored and then that discrepancy becomes the norm.
As time progresses another discrepancy might pop up-not significant enough to cause concern but still a legitimate discrepancy indeed. Something as small as one missing screw on a panel of 18, or cracked glass on a pressure gauge, a loose clamp on a pipe, a small vibration on a pump. Once the item of minor concern becomes ignored, it adds up over time until bigger and then bigger issues multiply. After a while, these “insignificant” problems: “holes in the Swiss cheese,” aligning to the point where a one-hour repair turns into hours or days of extended downtime from a culture of lack of ownership.
Scheduling time to perform Gemba Kaizen walks through the maintenance shops, machinery rooms, facilities and other areas is crucial to implementing a predictable operation. While on Gemba walks, create customized checklists for various systems instead of inspecting a piece of machinery as an entire entity. This will enable a sharp focus and enable the identification of problem areas with minimal distraction. The manager should take time to tour the less-frequented areas and “hard-to-get-to” areas. From experience, these areas are notorious for collecting trash and becoming fire hazards. In addition, these locations tend to have the most deterioration from corrosion and leaks simply due to their location. As a maintenance leader, take some time to walk out to the trash receptacles, staging areas, storerooms, flammable lockers, rooftops and any and all areas where small issues could be ignored and then raise the standard.
WATCH: How process excellence transforms maintenance and asset performance
Tackling reliability
When conducting any type of maintenance whether it be preventive maintenance corrective maintenance or modification, typically a technician will review the work order, consider safety precautions, follow the lockout tag out procedures and then remove and repair/replace a component. How often does the technician inspect his or her own work by not only considering the affected work area but the area in an 18-inch perimeter around where they were performing the procedure? This “best practice” of using an 18-inch rule can reveal other existing problems not otherwise discovered. It promotes good maintenance practices by using a rudimentary approach to inspect the work area and identify other issues as well as give a good cleaning to enable easier problem identification.
Furthermore, with the 18-inch rule in mind, it can be applied to a machine or piece of equipment that is taken out of service. When access panels are removed, it is an excellent opportunity to give it a more thorough inspection and cleaning to locate problem areas not otherwise possible.
Lack of information or technical data is the Achilles heel when it comes to root cause analysis. To thoroughly investigate trends, the first place to look would be in the maintenance records. How many times has the discrepancy occurred? When it did occur, how well did the technician document the findings? Were photos attached? Were measurements taken? Was the failure clearly articulated? To apply the concept of root cause elimination, it is impossible unless you can begin eliminating symptom by symptom, the failure modes of the equipment.
A best practice of a maintenance manager is to impress upon the technicians the importance of clear and concise documentation and inclusion of data points as they apply to torque, pressure, tension, vibes and so on to be used for data analysis in the spirit of reliability centered maintenance. Moreover, one of the most common FDA findings cites improper or lack of documentation and failure to document per SOPs.
“It’s amazing what you can learn when you read the book!” One of my first supervisors imprinted that in my mind in my younger years as a maintenance technician. Back in those days, I would pride myself on how fast I could diagnose and repair a defective piece of equipment. However, after troubleshooting “my way” using tribal knowledge instead of procedures written in the technical manuals or local procedures, I would find myself lost and compounding the issue rather than repairing it in accordance with the manual. Repeatedly, my supervisor would come around while I was performing a task and ask me where the manual was until it became gospel.
As a maintenance leader, how high do you prioritize the technicians utilizing tech orders, IOM's another reference material to troubleshoot diagnose and repair? Also, is the reference material up-to-date? Are SOPs regularly reviewed and revised to meet changing conditions? When was the last time revisions were verified to be current? It is astounding to find commonplace valuable reference material in a box in a corner or in a cabinet buried behind coffee mugs, spare parts and in drawers. Once again, centering on efficient effective maintenance focused on safety, predictability and reliability, and having accessible up-to-date reference materials are yet another key element of achieving this.
Even when the entire operation is running smoothly, equipment in service is at an all-time high, there is always room for improvement. By incorporating a continuous improvement approach focused on the customer, it gives the opportunity for everyone to voice their ideas. It equips the leadership and technicians with the necessary tools and skills to take Gemba walks, apply Lean Thinking, review failure data, identify trends, report near misses, identify bottlenecks, perform process mapping and write standardized checklists – all of which contribute to reliable processes, equipment and procedures.
In your organization, is your operations director willing to listen to your newest member of the maintenance team? Does the plant manager make routine tours of the equipment areas, backrooms, storage facilities and have discussions with the employees? Does the maintenance manager conduct recurring 1:1s with the team and receive feedback to improvement opportunities? These key questions and many more provide indicators concerning the pulse of an organization.
Efficient and effective maintenance
Fast forward 18 to 24 months and imagine taking a tour through the machinery rooms and seeing pipes clearly labeled, clean equipment, free of leaks, no missing or loose hardware, obvious examples of standardization regarding placement of absorbent material, a visual workspace with checklists, hazard areas clearly identified, eye wash stations, fire extinguishers, emergency stops all easy to locate. Safety data sheets readily accessible, PPE clean and available for use. Visual cues to identify tracking of qualifications, cross training, certifications with expirations. Clean and organized parts storage that is tracked, monitored and replenished as necessary, flammable lockers installed with grounding straps, contents on the inside clean and organized, labels placed on secondary containers and so on. All these examples are indicative of an organization that takes pride in ownership, empowers their employees to suggest improvements and insists on high standards – all of which contribute to an efficient and effective maintenance team.
How process intelligence transforms manufacturing & supply chains: 2025 industry report
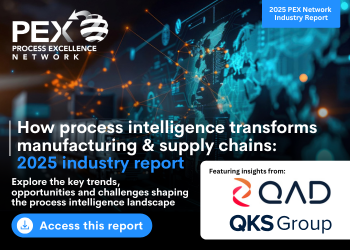
This industry report examines how and why organizations are investing in process intelligence to enhance manufacturing and supply chain management. “Global manufacturing and supply chains face enormous volatility in 2025,” says Michael Ochi, director at QAD. “Individual organizations feel tremendous pressure but also have new opportunities to grow. Any combination of protective and expansive business strategies requires constant speed and awareness.”
Organizations with significant manufacturing and supply chain operations are turning to process intelligence because it is uniquely capable of providing speed and awareness to any part of the business that leverages software.
Download the report to explore:
- The top five trends shaping process intelligence.
- Case study examples of process intelligence transforming manufacturing and supply chains.
- The key success factors and challenges of process intelligence adoption