Gemba in OPEX and continuous improvement
Gemba has unlimited resource capabilities when effectively utilized
Add bookmark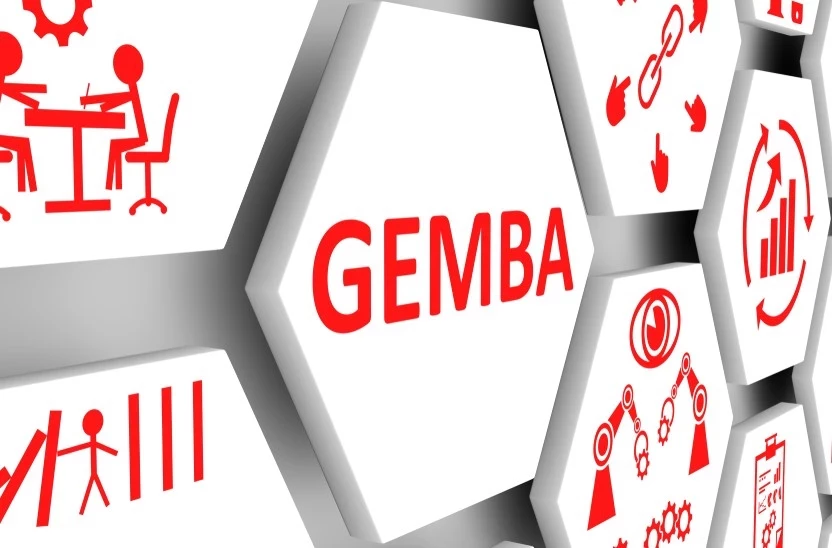
In today’s manufacturing operations, more and more leaders have become dependent on advanced technology to communicate with those in their network. Management information systems (MIS) and computerized maintenance management systems (CMMS) are at the core of our ability to receive and interpret information. We input requests and generate reports on production, expenditures, quality, customer feedback, scheduling and a labyrinth of additional information.
We have incorporated artificial intelligence (AI) and now we are so productive that many of us are creating more work to fill the voids in time we created from our own super-efficiency. As a result of this technology and automation, leaders tend to spend more and more time at their workstations reviewing documents and reports and then perhaps participating in Teams and Zoom meetings to discuss proposed solutions and ideas.
They fire off e-mails and texts throughout the day. They take their mobile devices to the break room, to get coffee, to the restroom, to lunch and even during their commute. While all this is going on, behind the scenes, work is being accomplished around the clock.
Frontline leaders, workers, craftsmen, technicians and specialists are all executing the roles they were hired to do as the autonomous machine continues to run perpetually. As leaders, we are dependent upon those in our reporting chain to execute their tasks, follow procedures, adhere to directives and comply with standard operating procedures as well as local, state and federal regulations. At the same time, we are held accountable to executives, board members and investors. Often, leaders at the director level and senior management may have a skewed perception of reality or compliance regarding what’s going on in the back shops or the production lines, manufacturing and maintenance areas. In this critical role, how can we really be sure that the areas we are responsible for are in compliance and employees are working in a safe, reliable and predictable environment?
Gemba in lean manufacturing
Gemba is the crucial first and most important concept in lean manufacturing. By now, we have all heard it, practiced and benefitted from it. It is certainly not a new concept; however, it may be silently fading into the sunset as we rely heavily on our digital sidekicks. Gemba has unlimited resource capabilities when effectively utilized – particularly useful for sustaining a culture of continuous improvement by exposing various forms of waste. When employed, it helps grasp a high level of understanding of a process, function or operation. It reveals issues in flow, safety and efficiency, exposing bottlenecks, overproduction and over or under-processing concerns with stock levels. It can also be a reasonable determination of the effectiveness of written procedures and adherence to policies.
Sadly, though, once an operation is functioning with a reasonable level of predictability and safety, Gemba only resurfaces when something goes wrong – and it is at that point that it becomes the star of the show.
Living in Gemba
I have practiced “living in Gemba” through several roles through the years. In one role, I was responsible for the repair and maintenance efforts of 54 shops with over 400 personnel in an aeronautical component repair facility. In another role, I was the aerospace ground equipment lead and in yet another, I was a quality manager.
Due to my position and responsibilities, I had to be the first one in the office to screen emails for potential pressing issues because my counterparts were on a different continent in several time zones. After filtering out the responses and tasks, I would review and highlight production reports for executive leadership and brief the operations director on the status of the top priorities. This was followed by two other meetings back-to-back as responsibilities trickled down the line.
After handling the administrative side and setting priorities for all shops throughout the day, I would grab my notepad and start walking. This part of my day had many positive aspects, including getting exercise by repeatedly going up and down several flights of stairs, greeting the tradesmen during their tasks, observing them while they went through various processes and asking questions about their workspace, the supply chain and any pain points. The transfer of information wasn’t like this at first. It took time to build a level of trust through repetition. Day in and out, I visited shops and got acquainted with the many professionals as well as the repair capabilities and each of the repair components. This was a stark contrast to the traditional visit by the maintenance manager, who only stopped by during abnormalities.
Power of Gemba walks
I have always had a thirst for knowledge, and this experience allowed me to learn about the inner workings of the latest aircraft engine components and modules, avionics systems and subsystems, navigation, all the different types and inner workings of ground equipment, life support systems and so on. The advantage of this wasn’t simply to quench my thirst for knowledge. I realized years later that it provided me with an invaluable perspective on interdependencies from shop to shop based on the components they worked with and the priorities they had to meet. I could take feedback from the shops and talk directly to decision-makers from logistics, facilities, warehouses and so on to break down barriers and enhance the organization as a whole.
As I gained a deeper understanding of how different parts of the organization rely on each other, trust between team members grew. I got to know their personal and professional goals, hobbies and interests. This helped create a sense of teamwork and they were more adept at addressing concerns. I became aware of the challenges they faced and the efforts they were putting in with the available resources. They trusted me to provide the necessary support to make their jobs easier and improve quality and efficiency.
This was the polar opposite of the environment I encountered as a young technician right out of trade school. Back then, we would see an individual from quality approaching us or one of the maintenance leaders headed our way and it was a quick scramble to clean up and hide or conceal in any other means to protect ourselves that we viewed as a threat. In retrospect, I wouldn't be surprised if those leaders back then had the same view of us before they even walked to the door.
Over time, that mentality went by the wayside and a feeling of optimism became apparent. Experienced managers and directors who focus on continuous improvement and operational excellence understand the importance of Gemba. This approach is highly effective and useful for staying connected with employees and building trust. By listening to people’s concerns, encouraging two-way communication and ensuring that information flows smoothly within the organization, managers can directly observe the effectiveness and efficiency of the operation which leads to confident decision making and improved predictability and safety.
All Access: AI in PEX is 2025
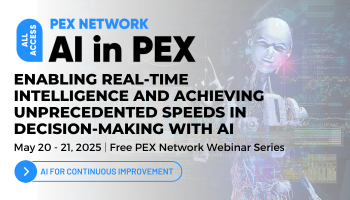
All Access: AI in PEX 2025 is designed to address these challenges and empower organizations to successfully integrate AI into their process improvement initiatives. The content series will bring together industry experts, thought leaders, and practitioners to share insights, best practices, and real-world case studies.
Register Now