How to run a Lean business
The Lean methodology is more relevant than ever, optimizing processes and supporting efficiency
Add bookmark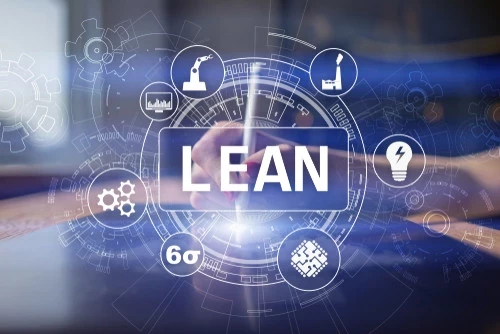
The Lean methodology is a set of practices and principles aimed at the optimization of business processes. It promotes two guiding values, continuous improvement and respect for people, which are distilled into five main elements: value identification, value stream mapping, efficient workflow, pull system and improvement. Lean aims to create optimal customer value while simultaneously fostering an efficient workplace that supports operational excellence.
The Lean methodology is an evolution of the Toyota Production System that the Japanese automaker implemented following World War II to improve the efficiency and flexibility of its manufacturing. It is similar to Kaizen, another continuous improvement methodology with roots in Japanese philosophy, and Agile, an approach to project management focusing on incremental, iterative steps.
Today, Lean is an approach applied by businesses in virtually all sectors, offering benefits that range from process enhancement and employee engagement to cost cutting and innovation.
Don't miss any news, updates or insider tips from PEX Network by getting them delivered to your inbox. Sign up to our newsletter and join our community of experts.
Lean is more relevant than ever
Lean remains a popular business model for organizations looking to maximize value by minimizing waste – be it time, resources or effort. “The Lean approach is more relevant than ever,” Alex Ugarte, operations manager of London Office Space, tells PEX Network. “With rising operational costs and increased competition – especially online – businesses invariably need to do more with less. Being Lean helps companies quickly adapt to market changes, meet customer demands more efficiently and maintain profitability by reducing unnecessary expenses.”
A Lean enterprise leader will optimize processes to boost value to customers, cut waste and make financial savings, says Jake Munday, CEO and co-founder of Custom Neon. Deploying a Lean business approach means looking at all facets of the business and determining which systems, processes and infrastructure are the biggest contributors to waste but also have the greatest potential for business value generation, adds Randy Shore, VP delivery and support at Kion.
READ: What is Lean?
Start with visibility
Gaining visibility is the first step you should take to adopt a Lean business model, says Shore. “Identifying your resources, how they’re being used and understanding what your processes are will give you better insight into the utilization and flow of your environment.” From there you can make educated decisions on where to apply automation or retire obsolete infrastructure or systems.
Taking the time to evaluate all business processes has worked well for Ashley Hainsworth, founder and director of Bed Kingdom. “It helps to analyze how well things are working and how you can make a process more efficient, reduce costs and add more value to the customer. From there, you should set achievable KPIs that you track, monitor and update.”
Build a Lean culture
For Scott Robinson, CEO of Unstack Software, installing a Lean culture has been a priority since he started running the company nine years ago. “This has been a focus since day one, so everyone knows to look for an alternative before making requests for big purchases. This is, arguably, the most important factor in running a Lean company. As the CEO, I can only make so many decisions, so I needed to instill this mindset in everyone on the team.”
Identify and eliminate waste
Identifying and eliminating waste – whether it’s time, materials or talent – is fundamental to the Lean approach. “This means streamlining operations and removing non-value add activities that consume resources without adding value for customers,” says Ugarte. It’s also important to clarify what “waste” means, adds Shore. “Waste is increasing carbon footprints via higher compute, overspending on underutilized resources or engaging in labor-intensive activities that divert team members’ attention to low-value tasks like maintenance.”
READ: The eight deadly lean wastes: DOWNTIME
Empower and train employees
Empowering employees to make decisions and take ownership of their processes fosters a proactive culture, and it’s an integral component of the Lean model. “It encourages innovation and accountability, which are essential for driving the Lean methodology forward,” says Ugarte.
In a Lean workplace, each worker’s contribution matters, adds Munday. “Change proposals are welcome from the team. Since everyone knows how much they contribute to our success, processes go more quickly, and participation and morale are higher.”
Ensuring the core team is skilled and understands each area of the business has been important at Bed Kingdom too, says Hainsworth. “We also focus on outsourcing non-core tasks to reduce our overheads and make sure that we can be as efficient as possible.”
Get everyone on board
“From my experience, the key to making Lean work is getting everyone on board, from the design team to the printer operators,” Paul Chow, CEO and co-founder at Design Dynamics, tells PEX Network. When everyone understands the core principles – eliminating waste, streamlining processes and continuous improvement – it becomes a team effort to constantly identify areas for efficiency. “We've seen a big difference in our turnaround times and material usage since implementing Lean. It’s not just about working faster, it’s about working smarter as a team.”
Focus on customer value
Customer focus is an essential element of Lean, with the goal of each process modification and optimization to enhance the client experience. “Every decision in a Lean business is evaluated based on customer value,” says Ugarte. “This customer-centric approach ensures that the product or service offering is finely tuned to meet current market demands.”
At Custom Neon, user feedback is constantly monitored and recommendations considered for continuous, iterative development cycles, adds Munday. “This alignment guarantees that we are very responsive to the demands and expectations of our market in addition to being incredibly efficient.”
Continuously improve
An integral component of a Lean organization is continuous improvement, with businesses thriving by constantly seeking ways to advance processes, says Ugarte. This involves regular reviews, audits of processes and the flexibility to adapt strategies that enhance efficiency and effectiveness.
“We evaluate our workflow on a regular basis to find inefficiencies and possible places where waste might be cut,” adds Munday. “To guarantee that resources are used as efficiently as possible, this calls for optimizing workflow, taking out pointless stages and streamlining procedures.”
Automate where possible
Effective automation is another integral facet of Lean, particularly in the modern, cloud-dependent business world. “Make sure you automate. I can’t stress this enough – automation is critical,” says Shore. Tasks like maintaining infrastructure, managing account provisions or other backend tasks are important, but are also time sucks when not automated. “Not to mention, they add no value to the actual business. I often see the cloud unlock so much potential for companies to innovate, improve customer experience or add new revenue streams. Getting rid of the mundane with automation is probably the most important step in becoming a Lean business,” he adds.
Adapt quickly and effectively
Lean businesses need to be able to react quickly and effectively, especially when it comes to risk management. “You also never know when things are going to change, so managing risk and having the capability to make quick decisions, be flexible and implement quick changes to your day-to-day operations and wider strategy is essential,” says Hainsworth.
PEX Report 2024 global state of process excellence
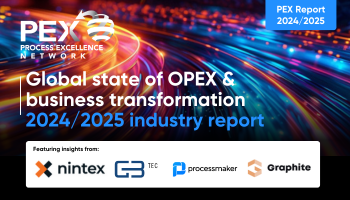
PEX Network's annual report reveals the current state and future trends of process excellence. Based on a study profiling hundreds of global process excellence leaders, the report provides insights on how to leverage innovation, generative AI, and process intelligence to achieve operational excellence, customer-centricity, and organizational growth. Download your copy of the PEX Report 2024/2025 today and benchmark your process excellence journey against your peers.
Download Now