Frost & Sullivan lists industrial automation priorities for 2025
AI-driven systems, cloud-powered analytics and ultra-fast connectivity are reshaping factory operations
Add bookmarkListen to this content
Audio conversion provided by OpenAI
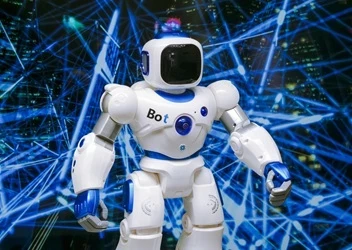
Frost & Sullivan released its latest list of imperatives reshaping industrial automation, highlighting the role of artificial intelligence (AI) systems, cloud-powered analytics and ultra-fast connectivity in reshaping factory operations and optimizing supply chains.
These advancements are not just improving efficiency – they are redefining manufacturing strategies, fostering innovation and creating new competitive advantages, the business consulting giant stated.
A recent study by IDS-INDATA revealed how the staggering financial and operational impact of unplanned manufacturing downtime emphasizes the critical need for digital transformation.
Don't miss any news, updates or insider tips from PEX Network by getting them delivered to your inbox. Sign up to our newsletter and join our community of experts.
7 industrial automation priorities for 2025
From autonomous production lines to predictive maintenance and human-machine collaboration, here are seven strategic forces accelerating this transformation, according to Frost & Sullivan.
1. Industry convergence and cross-sector synergy
Global automation hubs are emerging as powerhouses of industrial collaboration, bringing together key sectors such as manufacturing, industrial engineering, IT and power management. “These hubs unite companies, governments and researchers to develop cutting-edge automation solutions, standardize best practices and accelerate the deployment of next-gen robotics.”
2. Machine vision with AI-powered quality control
AI-driven machine vision is revolutionizing quality control, detecting microscopic defects with unmatched precision across automotive, electronics and pharmaceutical industries, Frost & Sullivan said. “For ecosystem players, this shift demands investments in AI-powered inspection, system upgrades and intelligent automation to stay competitive.”
3. AI-driven predictive maintenance
Factories are eliminating costly unplanned shutdowns with AI-driven predictive maintenance. “Smart sensors and AI algorithms analyze real-time equipment performance, predicting failures before they occur. This shift extends machinery lifespan, cutting repair costs and ensuring uninterrupted production cycles.”
Join us at All Access: AI in PEX 2025 and explore achieving unprecedented results with AI
4. Cloud-based automation with advanced data analytics
Cloud-powered automation platforms are revolutionizing industrial efficiency by centralizing robotics, AI and internet of things (IoT) data, Frost & Sullivan stated. “These systems provide real-time insights, allowing manufacturers to optimize operations, track performance remotely and scale automation with agility.” As cloud ecosystems evolve, the focus is shifting toward edge-cloud integration, AI-driven analytics and cyber security enhancements, enabling smarter, faster and more secure industrial automation.
5. Supply chain optimization with real-time data analytics
Supply chains are getting smarter through predictive analytics with AI-driven forecasting reducing inefficiencies, preventing stock shortages and ensuring just-in-time deliveries. “Businesses are leveraging real-time insights to make their logistics networks more agile, cost-effective and resilient to disruptions.”
6. Strengthening industrial communication with 5G connectivity
5G technology is unlocking ultra-fast, real-time industrial communication. Robots, IoT devices and cloud systems are now operating with near-zero latency, enabling hyper-efficient factory synchronization. “This game-changing connectivity is driving unprecedented levels of automation, precision and scalability.”
Register for All Access: Digital Adoption 2025 to learn how to create a successful digital adoption strategy
7. Digital twins and autonomous production lines
Finally, while AI-driven automation is transforming factories, digital twins take it further by creating virtual replicas for real-time simulation, predictive maintenance and process optimization, according to Frost & Sullivan. “This fusion of smart production and digital modeling slashes lead times, enhances efficiency and boosts operational resilience.”
Unplanned downtime is a strategic risk
For any organization, unplanned downtime is a strategic risk, commented Iain Davidson from Wireless Logic. “It can shorten machinery lifespan, increase costs and disrupt production across the business. As networks become more complex and devices more distributed, relying on reactive maintenance alone is no longer enough.”
Mitigating these risks means building automation and resilience into environments from the start. AI-driven predictive maintenance tools can spot unusual activity early, preventing failures at a speed that manual monitoring simply can’t match.
“Embedding high availability, security and automation into every layer helps minimize disruption and protect productivity,” Davidson added.
The aforementioned IDS-INDATA study indicated that UK and European manufacturers will lose more than £80 billion due to downtime in 2025, highlighting the urgent need for industries to adopt predictive maintenance and digital strategies to combat aging infrastructure, cyber vulnerabilities and supply chain disruption.
PEX Report 2024 global state of process excellence
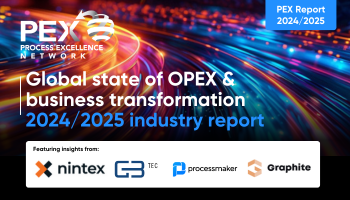
PEX Network's annual report reveals the current state and future trends of process excellence. Based on a study profiling hundreds of global process excellence leaders, the report provides insights on how to leverage innovation, generative AI, and process intelligence to achieve operational excellence, customer-centricity, and organizational growth. Download your copy of the PEX Report 2024/2025 today and benchmark your process excellence journey against your peers.
Download Now