Driving operational excellence through analysis, optimization or automation
Discover Software AG’s three-step process for driving operational excellence in your organization
Add bookmark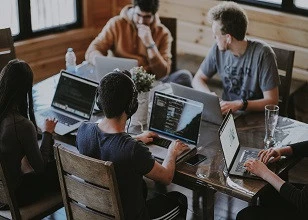
As Software AG has recently published an ebook on the megatrends in business transformation and operational excellence, I would like to look at the main intersections of these megatrends, the ‘Times Squares’ of the business world, where many initiatives converge. In this post, I will take a closer look at the relationship between process excellence and process automation.
Process excellence is often used synonymously with operational excellence, but it focuses more on the journey than the destination. Process excellence encompasses all initiatives, methods and technologies that are aimed at optimizing the performance, of elements such as time, costs and quality of a company's core processes.
In recent years, the trend toward automation of processes and tasks has intensified significantly. The technologies behind it are quite diverse and Gartner has created the term ‘hyperautomation’ for "a business-driven approach that allows organizations to automate business and IT processes through the orchestrated use of multiple technologies and platforms".
Trend map for process excellence, automation and Industry 4.0 – (Source: Software AG)
Automate business processes
Essentially, there are three relevant types of automation technology:
- Workflow automation and digital process automation (DPA): These practices focus on more complex, end-to-end processes and ensure that all tasks are executed in the correct logical order and by the appropriate employees and roles.
- No-code and low-code platforms: These are visual software development environments that allow even citizen developers to create business applications that are not overly complex.
- Robotic process automation (RPA): Software robots imitate human users, automating the repetitive and routine tasks of office workers by manipulating data and processing transactions within software applications.
Automation is a major trend, but it is too easy to think of achieving business value purely through automation. It can result in a patchwork of inconsistent, uncoordinated technologies, which is a horror scenario that you should avoid at all costs. Automation without prior optimization is like sitting in a Formula One car with a 20 horsepower engine and having only a vague idea of the destination of your journey.
It is a mistake to give citizen developers powerful tools for automation without understanding the underlying processes, the optimization goals and the compliance rules to be respected. Automation is not a silver bullet. Instead, it makes much more sense to follow the procedure of analyze, optimize and finally automate.
Analyzing processes and tasks
All three of the automate, analyze and optimize phases deliver significant business value, however, before implementing automation you need a good understanding of both your existing business processes and the new way of working. The appropriate technologies for finding this understanding are now available. If you look at the trend map, the monitoring of the real execution of tasks and processes plays a prominent role:
- Process mining analyzes, in an automated way, the as-is execution of end-to-end business processes to identify bottlenecks and to derive optimization measures.
- Task mining is the automated discovery and analysis of user interactions on a desktop, meaning the tasks being performed by a single employee.
The combination of process mining and task mining makes a lot of sense, as complex process steps can be analyzed and detailed through task mining. The combined results of process mining and task mining provide a perfect basis for identifying weaknesses along the entire process and at different levels of detail.
Optimizing business processes
When weak points are analyzed, you need to think about all aspects of optimization before automating processes. Often, organizational disruptions with waiting and idle times are one of the primary reasons for long throughput times of processes. In addition, for almost all companies, the lack of data integration across business functions is a major obstacle to the successful use of automation technologies.
In many companies, the level of process understanding and the integration across organizational units are quite low, with Forrester naming this “the tremendous collective debt within organizations”. Improving visibility of the actual performance of business operations is another basic prerequisite for improvements. Modern companies provide a digital handbook with an accurate model of the way of working to all employees across the organization to ensure that they understand their specific role and responsibilities.
Process excellence requires constant monitoring and analysis to improve and streamline the processes before and after automation. To succeed, you must have a plan to use mining, analysis and automation technologies together and to use the methods and technologies along a continuous optimization cycle. Many companies use the term ‘enterprise management system’ for this lifecycle, which you can read more about in my previous blog post.