Why process mining has reached the ‘must-have’ tipping point
Discover why process mining has become a ‘must-have’ for process analysis and optimization
Add bookmark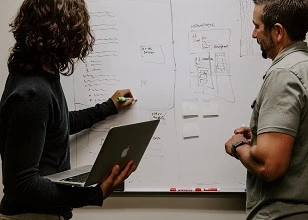
Since the turn of the millennium, process mining tools have emerged as a category of software that analyzes the execution of business processes and identifies vulnerabilities. We have now reached the tipping point where this technology has become indispensable for process-driven enterprises.
Learn more about the process mining basics here.
Process mining is based on the approach of reconstructing each process instance from transaction data, which is extracted from IT systems. These processes can be visualized as individual instances, and process executions can be aggregated and filtered according to any criteria. Of course, all metrics relevant to process performance in terms of time, cost and quality are measured.
What are the success factors that have recently helped this technology to achieve a breakthrough? The success is primarily based on the ten following aspects.
1. The methodology enables the analysis of processes across system boundaries, for example, with interrelated process sections that are executed in different IT systems, reconstructed and visualized as end-to-end processes.
2. As a result of increasing automation, significantly more analyzable data is available than was the case in the past. In particular, online sales processes now provide data on all relevant customer touchpoints.
3. The generation and visualization of actual processes and the analyses based on them are automated without manual effort through automated process discovery.
4. In contrast to classic business intelligence systems, the analysis goes far beyond the calculation of metrics, with key figures indicating problems as the "tip of the iceberg" and the root cause analysis performed by looking at the structure of processes. The greatest optimization potential usually lies in the elimination of unnecessary loops, complicated special cases and overabundance of process variants.
5. The automated analysis of variants provides a significant contribution to the elimination of quality, cost or lead time problems as evidenced in the image below, which illustrates the recognition and analysis of process variants.
Recognition and analysis of process variants (Source: Software AG)
6. As important as the standardization of processes is in terms of cost optimization, personalized products and services are crucial for success in many industries, such as special credit cards or loan offers from financial companies. This individualization can only be achieved by automating processes and permanently monitoring and analyzing all process variants.
7. Root-cause mining and machine learning algorithms make it possible to identify weak points in the process, determining the influencing factors and their combinations. Current research aims to shorten the training phase of the algorithms and to identify not only correlations but real causalities in the process data.
8. The range of scenarios for process analysis has expanded significantly. While in earlier years the focus was on 'classic' processes such as order-to-cash and purchase-to-pay, companies are now also using process mining to optimize production-related processes, linking IT data with operational technology data.
9. Competitive success is increasingly based on operational excellence and less on the pure quality of products. Many business models are based on superior mastery of processes such as quick commerce or fulfillment services of sales platforms. Customer loyalty can only be ensured through process excellence.
10. Process management is based on an optimization cycle between transformation, optimization and control. Process mining results can now be used to automatically simulate ‘what-if’ scenarios, such as if the BPM life cycle were completely closed, and derive optimization proposals based on them.
When it comes to the question of which aspects are optimized on this basis, a distinction can be made between three categories.
Internally, the focus is on efficiency issues, such as the analysis of cost, often in connection with processing times, but also the quality of the results along a process, since poor quality or negative check results often trigger multiple instances of processing and further cost.
For the customer, all aspects that influence customer satisfaction are of interest, such as reaction and throughput times in service or support processes. Even more relevant is the detection and elimination of outliers which, even if they occur rarely, have a massive negative impact on cost and customer satisfaction.
In many industries, regulatory requirements are increasing sharply, so compliance analyses play a major role as a third category. With an automated monitoring system, controls are integrated into process handling, and it is ensured that specifications regarding quality, data protection and risk management are adhered to for each individual processing operation or that deviations are detected automatically.